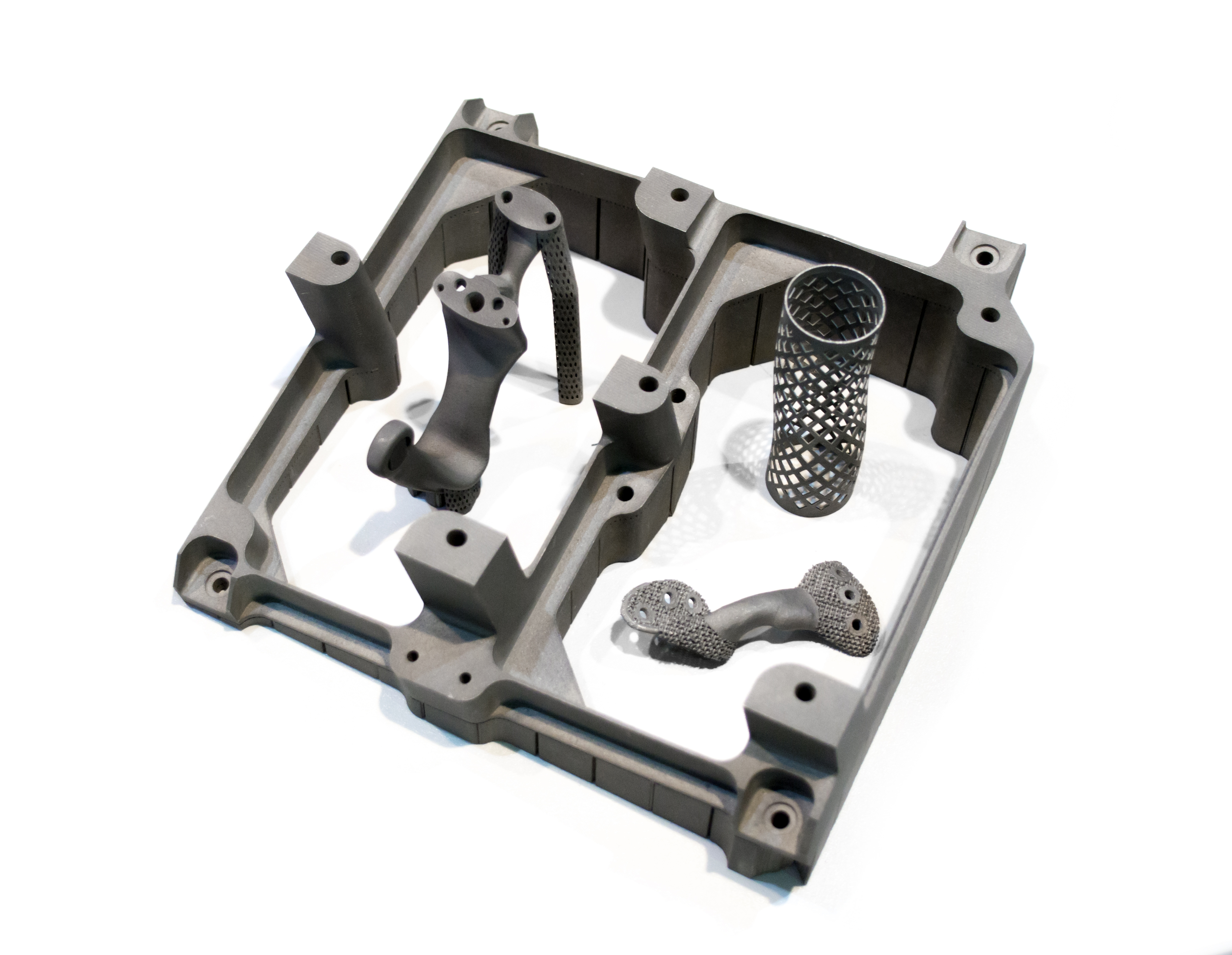
Design to print
Submitted by:
Sara Waddington
In the April 2025 issue of ISMR, we outline the benefits, challenges, growth forecasts and new design possibilities for manufacturers from the adoption of additive manufacturing technologies.
======
The COVID-19 pandemic highlighted the vulnerability of global manufacturing supply chains and the need to develop technologies and methods to support disruption-resilient manufacturing. One such resilient technology is additive manufacturing (AM), the process of creating a physical model of a digital CAD 3D model by building up layers of material using a 3D printer. Compared with 3D printing, AM is typically associated with industrial and manufacturing applications.
However, AM is not a stand-in for traditional manufacturing methods but a new way of looking at product design. It enables manufacturers to create designs that could not be produced using traditional manufacturing processes. Prototyping applications are prevalent, as additive manufacturing allows for quick iterations and design improvements. Industries such as aerospace, automotive, healthcare, energy and consumer goods are embracing additive manufacturing to streamline production processes, reduce waste and enable complex designs that were previously unattainable.
AM is a rapidly evolving field; parts can be designed faster with increased flexibility, better materials and optimised efficiency. It can also provide reduced product lifetime ownership costs through more efficient products and reduced through-life maintenance. Sustainability benefits come through the efficient use of materials and new supply chains. Common metals employed include steel; titanium; aluminium and cobalt chrome alloy. Additive manufacturing metals typically come in powder form, either as loose powders or bound together with a binder material.
“Metal additive manufacturing holds the potential to revolutionise the way we manufacture products and reduce material waste, energy consumption and transportation emissions, while also enabling the production of lightweight and complex parts that would be difficult or impossible to produce using traditional manufacturing methods. Metal AM technologies play an important role in improving the sustainability of a range of industries including the production of lightweight parts in aerospace, automotive and medical industries,” commented Cranfield University.
AM process categories
Although some media sources like to use the term “3D printing” as a synonym for all Additive Manufacturing (AM) processes, there are lots of individual processes which vary in their method of layer manufacturing. Individual processes will differ depending upon the material and machine technology employed.
There are several additive manufacturing technologies used in the market. These include stereolithography; fuse deposition modelling (FDM); direct metal laser sintering (DMLS); selective laser sintering (SLS); inkjet printing; polyjet printing; laser metal deposition and electron beam melting (EBM); digital light processing (DLP); laminated object manufacturing and others.
The American Society for Testing and Materials (ASTM) group “ASTM F42 – Additive Manufacturing” has formulated a set of standards that classify the range of Additive Manufacturing processes into seven distinct categories. These are listed below.
To read the rest of this article in the April 2025 issue of ISMR, see https://joom.ag/b6jd/p18