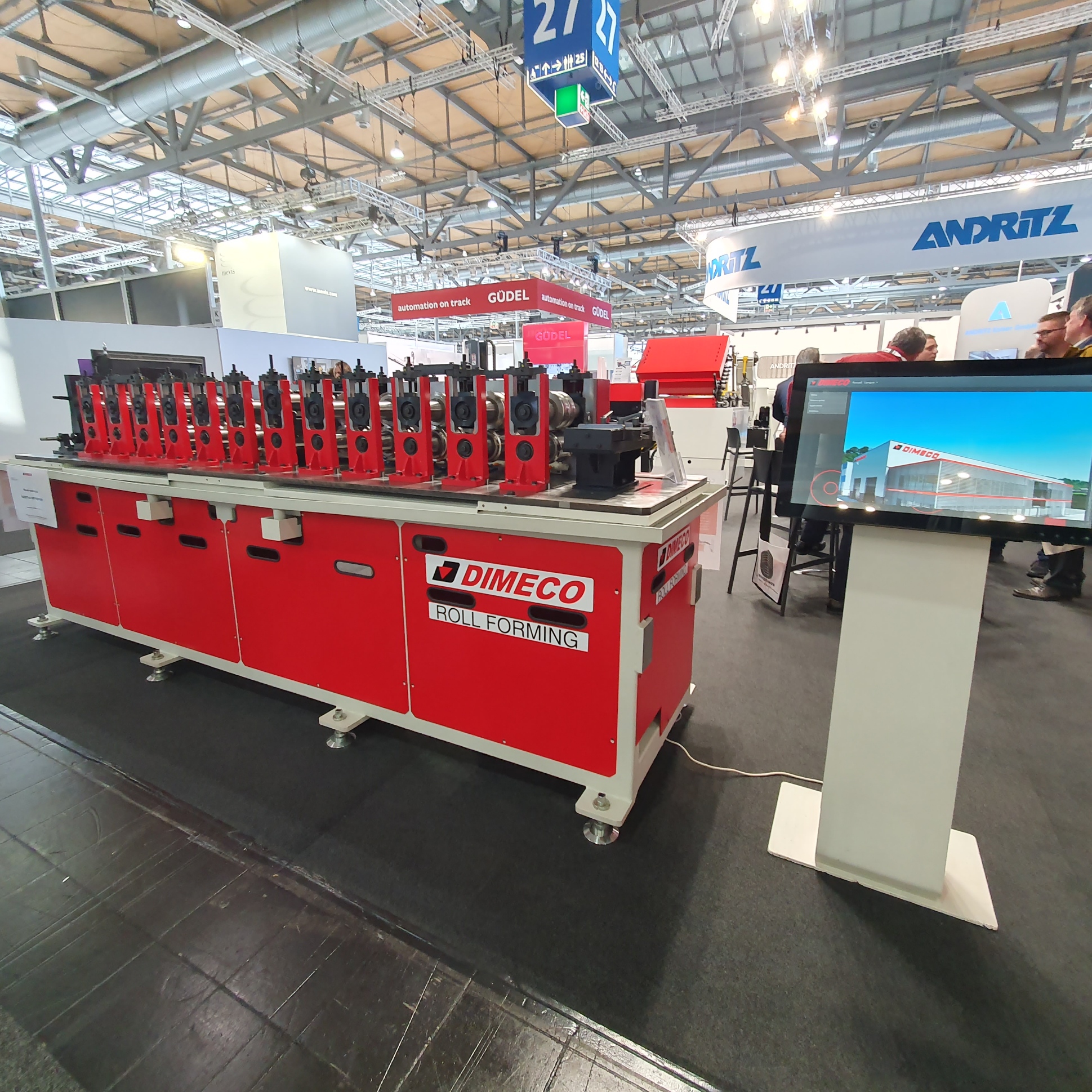
Roll forming in focus
Submitted by:
Sara Waddington
Roll forming is considered a highly cost-effective way to produce robust, multi-functional shapes in large quantities. We outline the benefits of the process for manufacturers.
=====
Roll forming is a process used for shaping metals such as steel, stainless steel and solid non-ferrous metals such as nickel, titanium and copper. It is a continuous process which converts sheet metal into an engineered shape using consecutive sets of mated rolls, each of which makes only incremental changes in the form. The sum of these small changes in form is a complex profile.
In roll formed parts, only a small amount of forming strain is put into the part during each station and even here, only a small section is bent at any given time. Because of this, more complex shapes can be achieved with an appropriately designed roll forming process. Roll forming has applications in many industry sectors including energy, construction, furniture, automotive, appliances, agriculture, solar and racking.
The roll forming process can not only manufacture typical shaped sections (such as channel, angle, boxes and round tube) but is also able to form more complex profiles required for demanding technical solutions.
The roll forming process
“In the forming process, a coil or long individual strips are fed through a roll forming line which converts the flat sheet to a contoured cross-sectional profile. The unique aspect of this approach is the use of consecutive forming stations, each of which nudges the metal towards the desired shape. Based on the targeted profile, a computer calculates the optimal placing and shape of the rollers for maximum efficiency and designs the track. The more advanced the desired shape, the more rollers the material goes through. The roll forming line can bend metal, form metal into tubes, create metal maze-like structures and punch the metal with holes during the process,” outlined materials specialist, National Material Company (NMC).
“The rollers are precision-contoured metal dies that shape the incoming sheet metal. In most cases, they are also the powered drive rolls that pull the strip through the roll forming unit. These rollers can be as simple as the cylindrical rollers used to roll luggage through airport scanners, or they can take on more intricate shapes. After the final forming station, the strip is sheared to the ordered product length. Typically, no additional work is needed before shipment, since the final form has been achieved,” it added.
Each pair of rollers further forms the metal strip until it reaches the desired cross-sectional shape at the end of the line, ready to be cut into the appropriate length. The more complex the profile shape, the more pairs of rollers required. The finished form is generally referred to as a rolled profile, roll-formed (custom) profile, custom profile, steel profile or metal section.
“In addition to open profiles, closed cross-sections can also be produced with roll forming. With joining technologies, such as laser welding and HF welding, the metal strip’s edges are brought together and welded shut. This is done as an integral part of roll forming, so that steel tubes with complex closed cross-sections can be produced cost-effectively,” added roll forming specialist, Welser Profile.
Counting the benefits
There are a variety of advantages to roll forming. Because of the “assembly line” efficiency of roll forming, long lengths of metal can be produced and cut in large quantities, which reduces cost. Secondary processes (such as punching or even welding) can be integrated into a single production line. The profiles that can be produced using roll formed sheet steel are similar to what is seen in extruded aluminium.
Custom profiles can be (re)produced in large lengths consistently, and with high quality. Additionally, since features such as holes, slots or embossing can be easily added during the forming process, roll forming is considered a highly cost-effective way to produce robust, multi-functional shapes in large quantities. Roll forming is a popular alternative to aluminium extrusion when the material properties of steels are required, or where adding the features into the aluminium profile is a costly secondary process.
To read the rest of this article in the July/August issue of ISMR, see https://joom.ag/41wd/p48