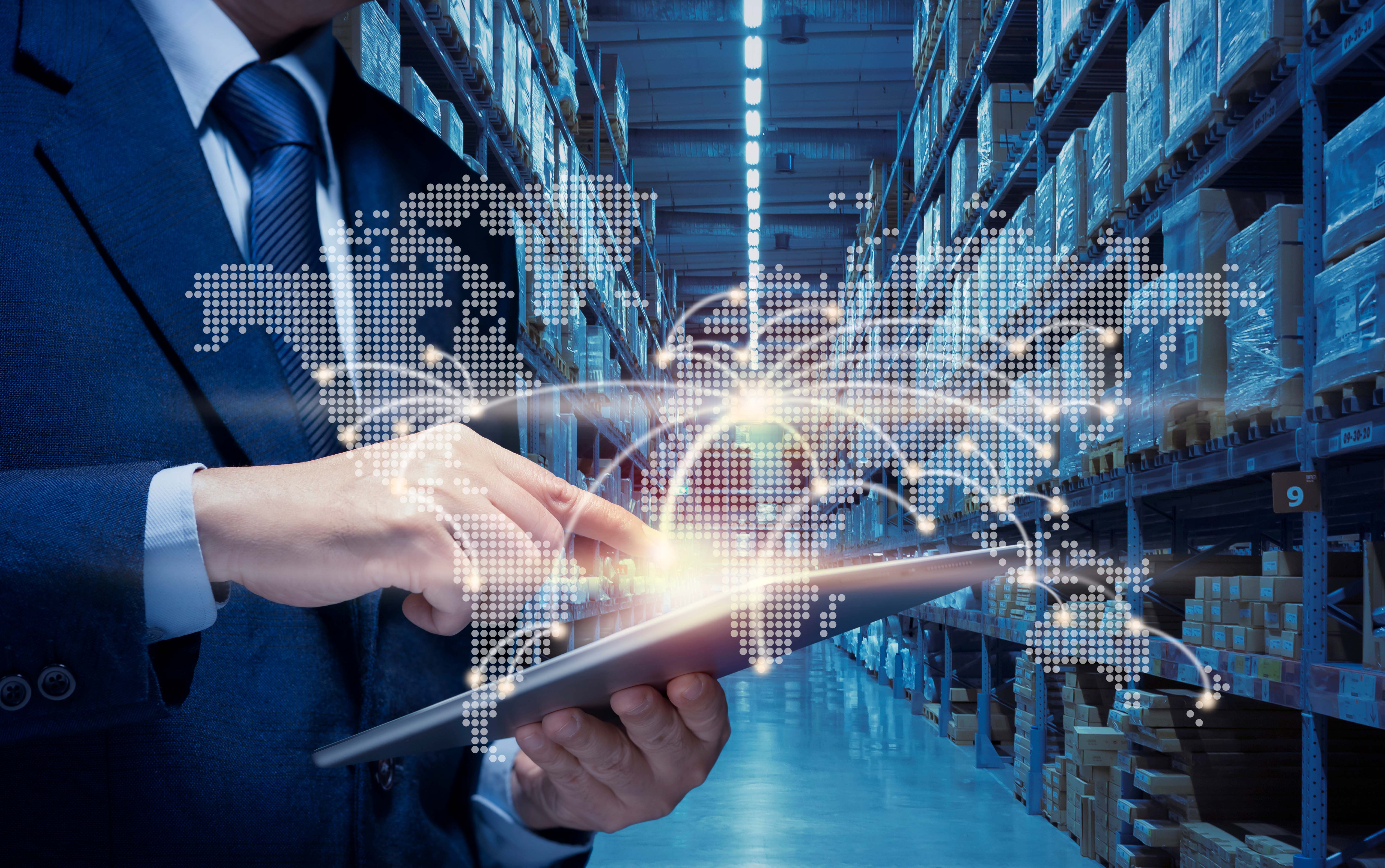
What does CBAM mean for manufacturers?
Submitted by:
Sara Waddington
In the March 2025 issue of ISMR, Simon Thompson explains that the European Union’s Carbon Border Adjustment Mechanism (CBAM) heralds a shift to sustainable business practices for manufacturers in the metals supply chain.
===========
The European Union’s Carbon Border Adjustment Mechanism (CBAM), that will end its transition period in 2026, is one of the measures put in place by the EU with the objective of combating climate change to become climate-resilient by 2050. By tightening its regulations and putting policies, legislations and strategies into place to prevent or minimise the impact of climate change wherever possible, the European Union is emphasising the importance of shifting to sustainable business practices.
With CBAM, the EU aims to counter the effect of carbon leakage which occurs when companies based in the EU move carbon-intensive production abroad to countries where less stringent climate policies are in place, or purchase from outside the EU for the same reason. The goods affected include iron, steel, aluminium, cement, fertilisers, electricity and hydrogen.
After the CBAM transition period, in 2026, importers of the goods subject to regulation will need to register with national authorities and purchase CBAM certificates, whose price will be based on the weekly average auction price of EU ETS allowances, expressed in €/tonne of CO₂ emitted. As a result, CBAM effectively puts a price tag (15%-30% price increase) on the carbon emissions embodied in certain imported products.
What does this mean for manufacturers?
CBAM’s ripple effect is significant and requires businesses to improve the way that they calculate the embodied emissions goods relying on greater supply chain transparency. This is particularly relevant for businesses producing and purchasing materials with a high carbon footprint, such as steel and aluminium, stressing the importance of supply chain traceability and transparency to accurately calculate emissions.
The bulk of many businesses’ carbon emissions is generated via the supply chain, especially in the form of Scope 3 emissions. These emissions are those that result from activities related to assets not owned or controlled by the reporting organisation, but that the organisation indirectly affects in its value chain both upstream and downstream.
Notably, 73.9% of steel production in 2023 was in Asia¹, where traditional Blast Furnace-Basic Oxygen Furnaces are used to turn iron ore into steel. There, furnaces have a high carbon footprint of 1.987 tonnes of CO₂ per tonne of steel produced², with a huge impact on final emission calculation.
In this context, procurement teams and suppliers need to work together to meet CBAM requirements by understanding emission reduction strategies, explore ways to minimise their carbon footprint and collect and verify all relevant data. A key instrument in guaranteeing this collaboration throughout all stages of the supply chain is technology, including AI and ML, applied to procurement solutions.
In fact, to accurately track the carbon emissions embedded in imported goods, procurement teams need a robust system that provides detailed reporting and monitoring at all stages of the supply chain. Building strong relationships with suppliers is essential to achieve this, and the right software can make collaboration much easier.
Furthermore, since it incentivises sourcing from suppliers with a low carbon footprint, CBAM is bound to benefit suppliers operating in regions with stricter environmental regulations (such as the EU and UK) and investing in clean technologies. This shift may also mean companies will relocate some production facilities, nearshore to reduce transportation emissions and directly collaborate with suppliers to adopt greener technologies and processes. For steel production, this will also mean moving away from traditional Blast Furnace-Basic Oxygen Furnaces to the eco-friendlier Electric Arc Furnaces that not only recycle scrap metal but rely on electricity, reducing steel production’s footprint to 0.357 tonnes of CO₂ per tonne³.
Tools for compliance
To read the rest of this article in the March 2025 issue of ISMR, see https://joom.ag/EKMd/p42