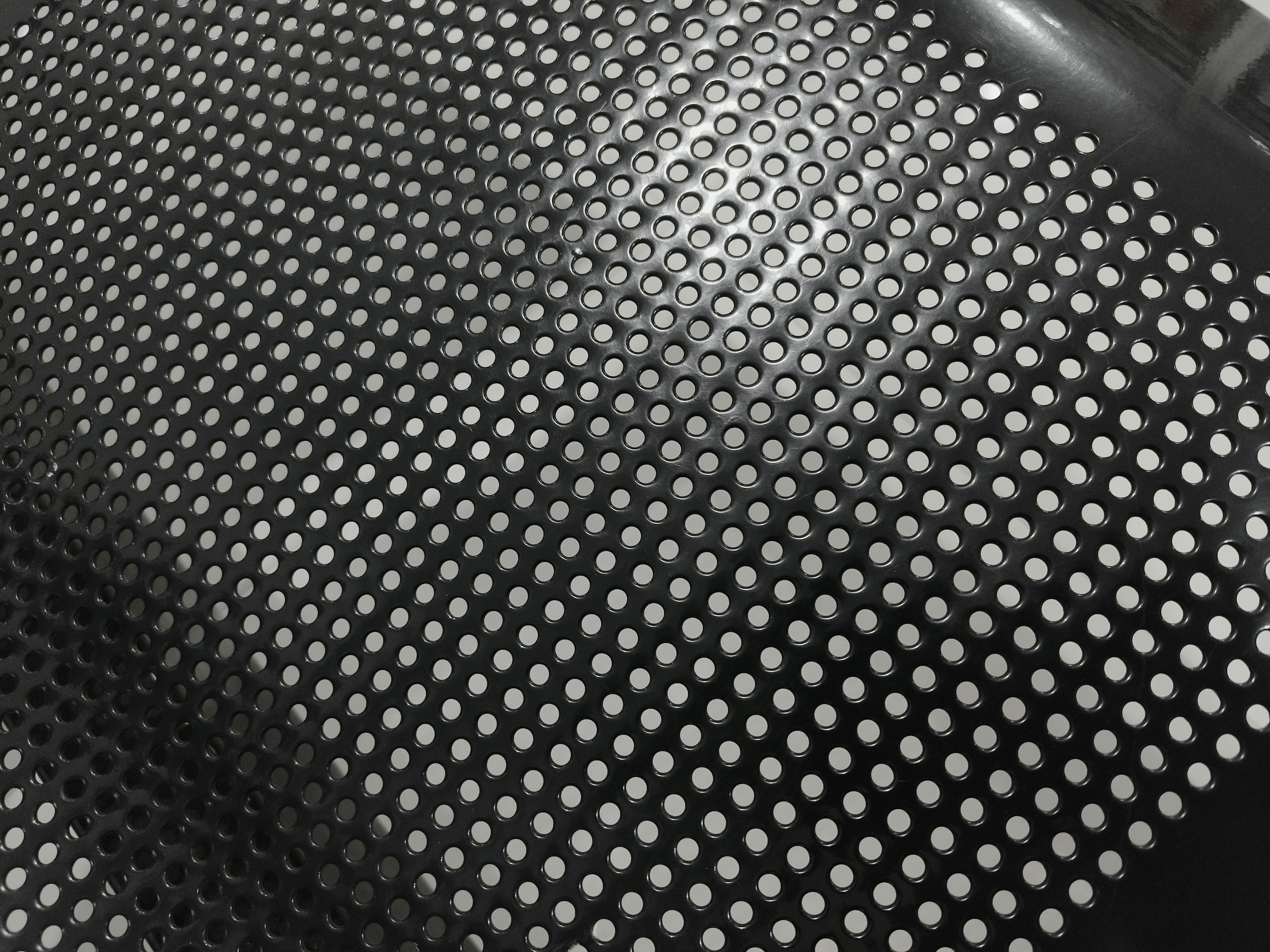
Packing a punch
Submitted by:
Sara Waddington
Greengate Metal Components highlights the techniques, machinery and materials involved in sheet metal punching, including the different types of punches and dies as well as the benefits and limitations of the process.
Sheet metal punching is an essential process in modern manufacturing, allowing the creation of precise metal components across a range of industries. From automotive parts to construction materials, this method helps to produce everything from simple holes to intricate shapes in sheet metal. Its flexibility and efficiency make it a popular choice for manufacturers needing high-volume production with consistent results.
CNC punching is an efficient solution for creating holes, slots or cut-outs in sheet metal. Using a programmed punch and die, this technique works very well for repetitive patterns and high-volume production. The method is particularly effective for parts such as enclosures, panels, and brackets, where speed and accuracy are essential. It supports a variety of materials and thicknesses, making it suitable for many industries. CNC punching can also combine multiple punches in a single process, allowing for intricate designs and high repeatability. It is widely used in projects that require scalability without compromising on quality.
In this article, we examine the techniques, machinery and materials involved in sheet metal punching. It will provide a comprehensive overview of punching, including the different types of punches and dies, the benefits and limitations of sheet metal punching and how to choose the right method for your production needs.
What is sheet metal punching?
Sheet metal punching is a manufacturing process that involves the creation of holes or shapes in metal sheets by applying force through a punch. The process begins by positioning the metal sheet between a punch and a die. Once in place, the punch applies force to cut out specific sections, either creating scrap material or forming a functional shape for the final product.
The punching technique is prized for its speed and accuracy, making it suitable for high-volume production. Industries such as automotive, construction and electronics commonly use sheet metal punching to produce uniform shapes in large quantities, giving consistency and efficiency across production lines.
The step-by-step punching process includes:
• Positioning the metal sheet between the punch and die.
• Applying downward force to cut the metal.
• Removing the scrap material or keeping the punched piece, de pending upon the design.
• Shaping or perforating the metal according to the required specifications.
This process is widely used in functional and decorative applications across numerous industries, offering the flexibility to handle a wide range of designs and materials.
Punching techniques
Several techniques are available for sheet metal punching, each matched to different applications. The choice of technique depends upon factors such as the complexity of the design, production speed and the accuracy. Here are some common techniques:
Single punching is the most basic technique, where a single stroke of the punch is used to create a hole or cut-out. It is suitable for simple shapes and is typically applied in low-volume production or when precision is more useful than speed. Common applications include the creation of brackets and smaller enclosures, where accuracy is paramount.
Nibbling involves a series of small, overlapping punches to cut out larger or more irregular shapes. This technique offers greater design flexibility, allowing the creation of intricate shapes that are difficult or impossible with single punching. However, nibbling can leave rougher edges due to the multiple punches, which may require additional finishing. It is often used for prototypes or custom parts that require more complex design features.
Perforating involves punching multiple holes into a metal sheet in a grid or pattern. This technique is commonly used to create perforated metal sheets, which are frequently found in applications such as filters, ventilation panels and decorative facades. Perforating can be done quickly, making it a suitable choice for high-volume production where uniformity and speed are key considerations.
Embossing is a variation of punching that creates raised or indented designs on the surface of the metal without fully piercing it. This technique is commonly used for decorative purposes or to add functional features such as grip or texture to metal components. Embossing is frequently applied in industries requiring aesthetically pleasing or ergonomically designed metal products.
Each of these techniques provides distinct advantages depending upon the required design complexity, production speed and material used. For example, nibbling allows for detailed designs, while perforating is suitable for high-speed production.
Common punching applications
Sheet metal punching is widely used across numerous industries due to its precision and efficiency. Below are some of the most common applications.
To read the rest of this article in the April issue of ISMR, please see https://joom.ag/b6jd/p44