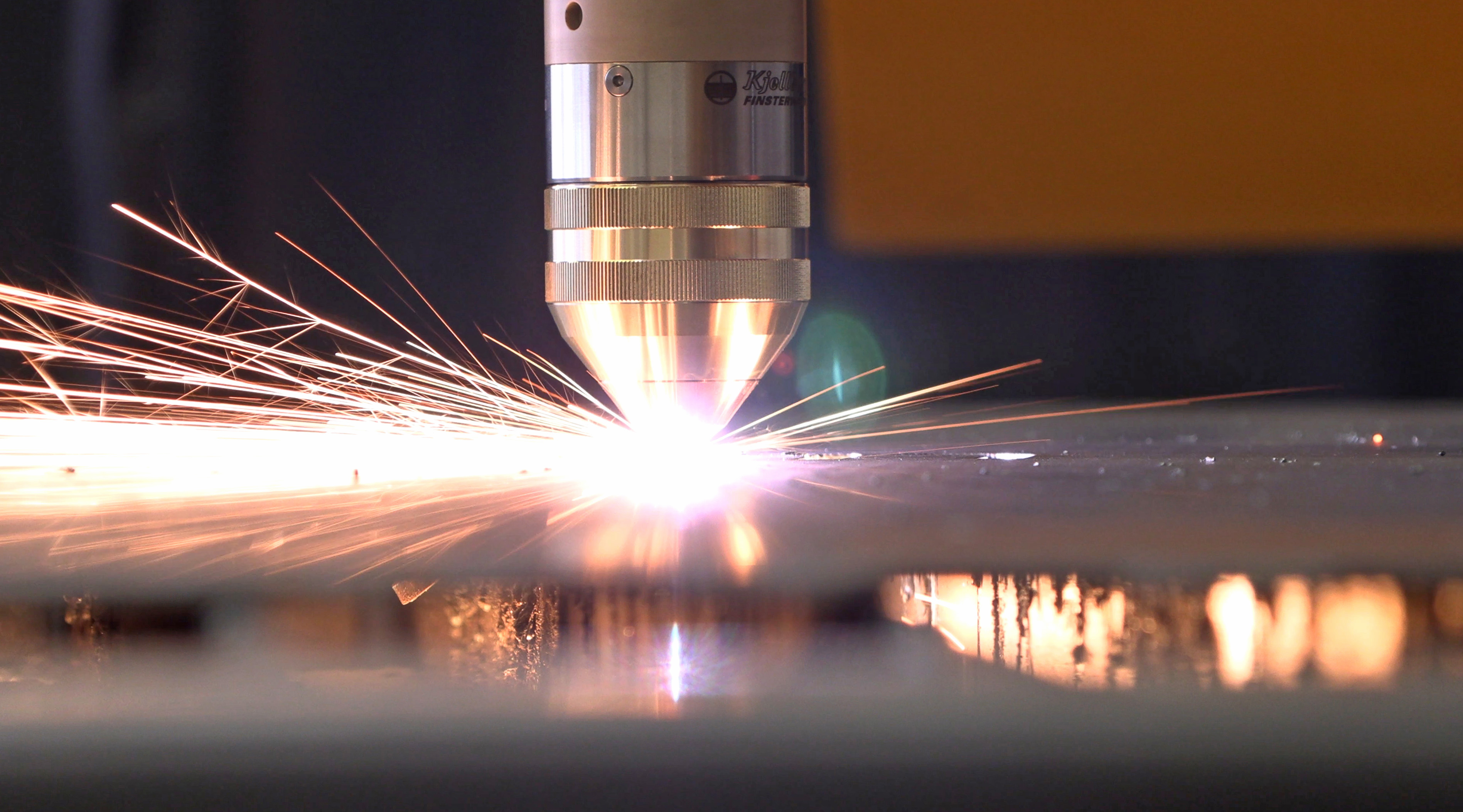
The power of plasma
Submitted by:
Sara Waddington
Plasma cutting is a high-speed process by which highly energised molecules can be harnessed to economically cut a variety of alloys in a range of sizes and thickness. This method of manufacturing is often found on factory floors that prepare metal components, such as those made from aluminium or titanium. It is an effective way of cutting both thin and thick materials.
Often used in fabrication shops, automotive repair and restoration, industrial construction, and salvage and scrapping operations, it is in widespread use by large-scale industrial CNC applications down to small hobbyist shops. Since plasma cutters produce a very hot and very localised ‘cone’ for the cutting operation, they are extremely useful for cutting sheet metal in curved or angled shapes.
This melting process of cutting through electrically conductive materials uses an accelerated jet of hot plasma. A jet of ionised gas at temperatures of above 20,000°C is used to melt and expel material from the cut. During the process, an electric arc is struck between an electrode (cathode) and the workpiece (anode). The electrode is recessed in a water- or air-cooled gas nozzle which constricts the arc, causing the narrow, high- temperature, high-velocity plasma jet to form.
Handheld vs mechanised plasma
Most handheld plasma systems consist of an inverter-based power supply (like most welders) that combines electricity and compressed (air as the plasma gas) to produce a plasma arc that is generated at the end of a hand torch. Handheld plasma systems require electricity, either from a line or a generator, and compressed air either from an air compressor or bottle.
Mechanised plasma cutting is an automated method for cutting carbon steel and a variety of non-ferrous metals in production-based environments. CNC plasma cutting machines usually incorporate a different type of plasma system than handheld cutting applications, one specifically designed for “mechanised” cutting instead of handheld cutting. Mechanised plasma systems use a straight barrelled torch which can be carried by a machine and have some type of interface that can be controlled automatically by the CNC.
Some entry-level machines can carry a torch designed for handheld cutting processes. But any machine designed for serious manufacturing or fabrication will use a mechanised torch and plasma system. Many plasma cutters can handle metals that are around 1-2 inches thick. Some can even handle metals up to 6 inches thick.
Plasma cutters are an excellent method for cutting through steel and other metals, but care should be taken when using this equipment. The appropriate safety wear (gloves, eye goggles, ear protectors, flame-resistant clothing etc.) should be worn. There should also be adequate ventilation when plasma cutting as the fumes can be a health hazard.
A flexible option
Plasma can cut all conductive materials, including carbon steel and non-ferrous metals. Plasma is also safer than oxy-fuel, which requires the use of a flammable gas. Plasma cutting is also generally faster than oxy-fuel cutting. On gauge materials, plasma cutting speeds are 12 times faster than oxy-fuel cutting speeds and on materials of up to 1”, plasma cutting speeds are twice as fast as oxy-fuel. Plasma also provides much faster pierce times which can greatly impact automated cutting productivity.
To read the rest of this article in the May issue of ISMR, see https://joom.ag/HBjd/p38