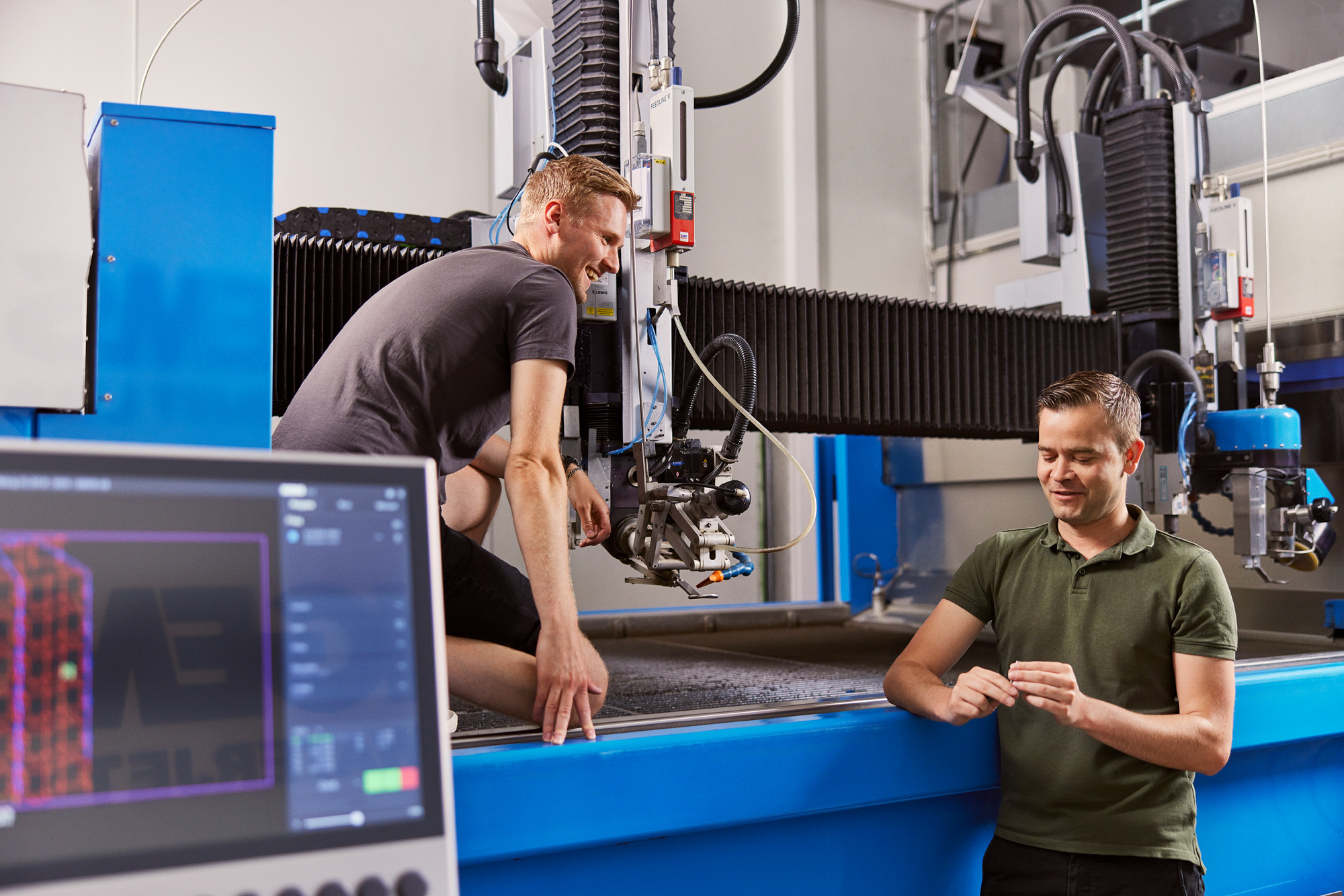
The water margin
Submitted by:
Sara Waddington
The waterjet process is recognized as one of the most versatile and fastest-growing cutting processes used in production applications across the globe. The versatile and efficient cold cutting process produces no heat-affected zones, thermal distortions, hardened material or material stresses. No noxious gases or liquids are used in waterjet cutting, and waterjets do not create hazardous materials or vapours. There is minimal material waste and environmental impact. A clean, burr-free finish often eliminates the need for secondary surface finishing.
Despite the high psi (pounds per square inch), waterjets do not actually cut with pressure but instead rely on velocity. The water pressure is exchanged for velocity when the water passes out of the cutting head’s orifice. The higher the pressure, the higher the stream velocity. Pure waterjet is the original waterjet cutting method. An abrasive waterjet adds a garnet abrasive fed into the cutting head, mixed with the pure waterjet stream, and used to cut hard materials. Adding abrasive to the supersonic waterjet stream increases the cutting power a thousand times.
With the ability to cut complex shapes and intricate details, waterjet cutting systems are compatible with multiple materials and thicknesses. Systems can be configured with multiple heads; five-axis cutting heads can produce continuous bevels, revolve around the workpiece and cut at angles from 0-90 degrees. Robotic waterjet cells; 3D cutting; nano jet cutting and micro waterjet cutting are examples of advances that will help to expand the market for waterjet cutting.
“Waterjet is often regarded as an ideal cutting solution for job shops. A job shop rarely knows which project will come through the door next, and the ability of waterjet to cut virtually any material at any thickness on the same system provides unparalleled flexibility for owners. A waterjet can support almost any project that comes through the door, allowing owners to expand their business, take on more work and provide a quick return on investment,” commented waterjet specialist, Flow International.
Below is a selection of the latest new and innovative waterjet technologies and products for sheet metal manufacturers, in alphabetical order.
Innovation in focus
AAG (AXYZ Automation Group) offers abrasive waterjet cutting systems that include the X-Series waterjet with the APEX 60 five-axis cutting head, M-series and A-Series waterjets. Its water-only series systems are the H-series, L-series and J-series. The company’s 105,000-square foot facility in Waterdown, ON, Canada, now houses its three brands (AXYZ, WARDJET and CNCSHOP) under one roof. Key attributes of the Apex-60 include five-axis cutting heads to offer of movement between 0° and 90°. This enables users to control taper angle and create complex 3D designs
WARDJET showcased its A-Series waterjet cutting system at the EuroBLECH exhibition in Hanover, Germany, in October 2024. The WARDJET A-Series waterjet cutter is a versatile and compact machine that can cut through most materials, from titanium to concrete. It does this in a small, enclosed footprint, making it suitable for businesses with limited floor space. Despite its small size, the A-Series is very powerful and can be used to cut intricate designs or to create custom parts or prototypes.
ACCURL’s five-axis MAX BP-C Series waterjet cutting system features a MAX 3D five-axis Bevel Cutting Head 2.0, new Hypertherm Echion 50 waterjet pumps and an anti-collision system). Collision Protection 2.0). It is controlled by an ESA S660 series CNC control unit. The MAX 3D cutter head has five axes (three linear and two rotating). It has been designed for both pure 3D cut and 2D 1/2 cut (flat cut with bevel), without losing 2D (flat) cut functionality.
The ACCURL MAX-WJCNC waterjet cutting series is an addition to ACCURL’s MAX-WJCNC waterjet cutting machine line. The ACCURL® Go beyond is a five-axis waterjet cutter for three-dimensional cutting at angles from 0° to 90°.
ALLFI produces high-pressure components for water jet cutting as well as high-pressure pumps, modular cutting head systems and robotic waterjet cells (in partnership with IDASA). The Quantum SPT™ Quantum NXT™ (electric servo pump) incorporates the core “direct servo” technology first used by NASA for the Space Shuttle programme by replacing obsolete hydraulic cylinders with new, compact, efficient and controllable servo linear actuators. Its DynaMAX and DaraMax are predictive waterjet pumps.
BFT GmbH offers energy-saving, high-pressure pumps and components for waterjet cutting applications. It has showcased two high-pressure pumps in its EcoTron range – the 40.37+ and the 40.45+. It also includes a Servotron, Vectron, Hypertron and Jetron range of high-pressure pumps. It now supplies to the U.S. market with an office in Merrillville, Indiana.
Luxembourg manufacturer CERATIZIT (part of the Plansee Group) has three distinct HyproJET product lines; the focusing tubes are designed for all modern waterjet cutting head systems and support automatic centring during mounting. In addition to its line of abrasive jet focusing tubes, it produces wear products out of variable carbide configurations (such as plungers for high pressure pumps; splash discs; catcher cups; inlet guides; wear plates; restrictor shields and inlet tubes).
CMS Metal Technology offers a wide range of complete three- and five-axis waterjet cutting systems, pressure intensifiers and dry or wet deburring and satin finishing machines. Since the 90’s, thanks to the acquisition of Tecnocut and continuous internal developments, it now boasts more than 1,500 installations worldwide. It launched its CMS Tecnocut Proline in 2021, a compact, sturdy single-block design waterjet cutting system that also features a pipe-cutting option.
Its new DDX EasyJet is a complete CMS suite that brings together several applications in one software to program machining processes quickly and easily. Other waterjet cutting models include the Tecnocut Aquatec and Tecnocut Waterspeedy s
Its digital solutions include CMS Connect, an IoT platform that is integrated with the latest-generation CMS machines, and CMS Active, its operator HMI interface, as well as the Eye CMS console. Its JD5 five-axis cutting head offers infinite rotation (continuous rotation of the C-axis during consecutive cuts), designed to reduce the tolerance error of "mirror"-cut parts to zero. To ensure that the cutting process is repeatable, CMS offers a TCP (Tool Centre Position) and focal distance laser measurement device on the five-axis head. CMS has also developed the Tecnocut e-pump, a new hybrid pressure intensifier. Other models include the Easypump and Jetpower Evo.
ConSus - ANT Stationary Cutting Solutions GmbH, a division of the ANT Group, has over 20 years of experience in mobile Water Abrasive Suspension (WAS) cutting. The central or decentralised processing of 80% or more of the abrasive with ANT's Abrasive Recycling Unit (ARU) significantly reduces consumption costs, it told ISMR. A continuous suspension jet, it said, provides a ‘more efficient cutting performance at lower pressure compared to conventional Water Abrasive Injection (WAIS) systems.’
Eckert AS Sp. z o.o. is a Polish manufacturer of CNC cutting machines, working across three technologies (plasma, oxyfuel and waterjet cutting) or combined technologies. Its Opal Waterjet cutting system features a wide range of equipment options, including a powerful ProX 3D cutting head. It is suitable for most materials up to 250mm in thickness.
Its Opal Waterjet Combo is a patented, rapid CNC waterjet for plasma and waterjet cutting. Equipped with the Pro-X 3D waterjet cutting head, it combines the advantages of ultra-fast plasma cutting and precision waterjet cutting.
To read the rest of this article in the May 2025 issue of ISMR, see https://joom.ag/HBjd/p52