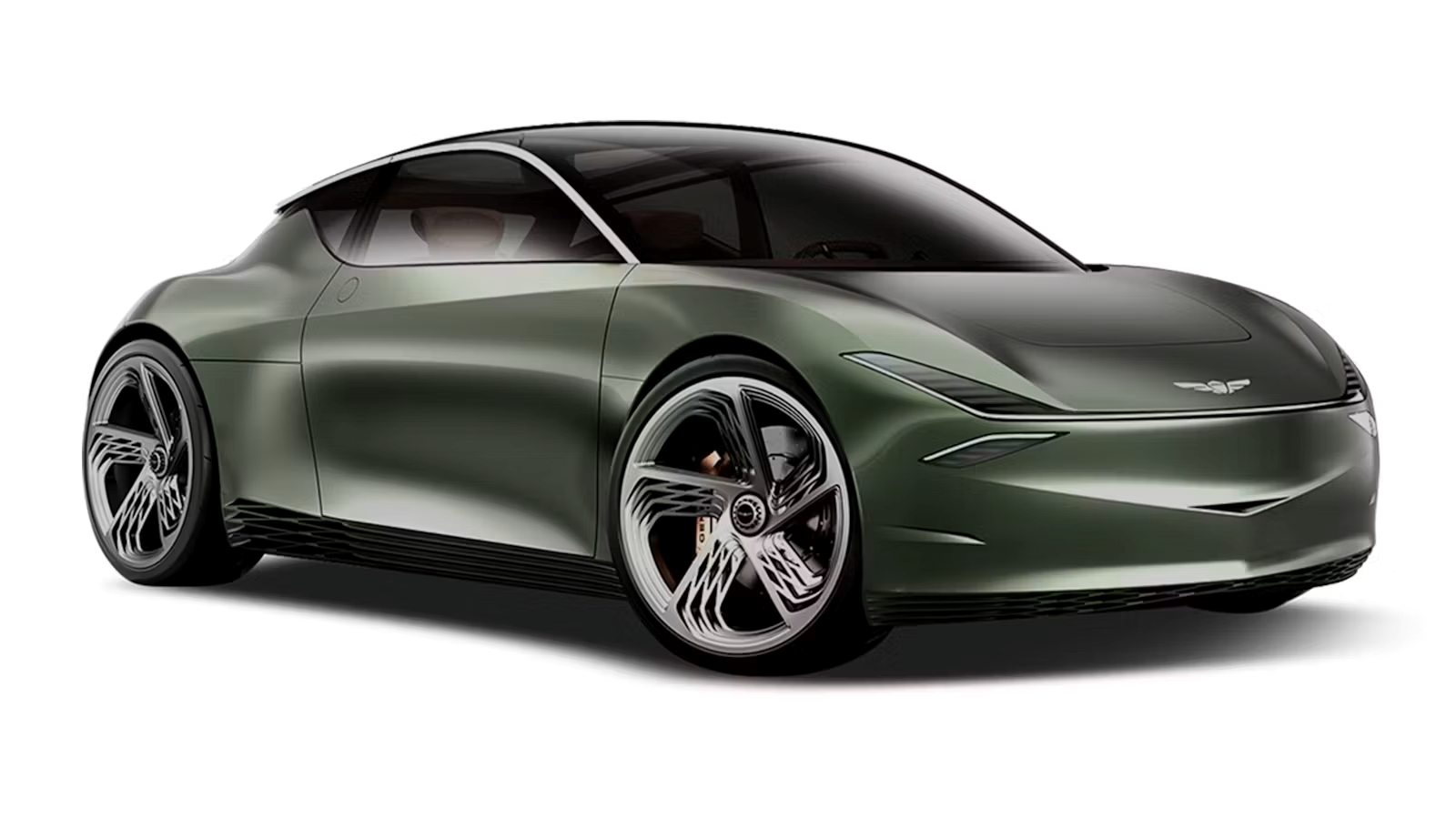
AI-powered shifts
Submitted by:
Sara Waddington
Hyundai Motor Group (HMG) recognized the need to implement artificial intelligence (AI) to enable a seamless shift left in the electric vehicle development process. Simcenter Engineering Services therefore created and trained a neural network to deliver simulation results that enable direct optimisation of Hyundai models.
============
In the vehicle development process, it is advantageous for companies to shift left in the V-cycle as much as possible. By avoiding late-stage design changes, engineering teams can achieve significant time and cost savings and help drive products to market faster.
Artificial intelligence (AI) is an increasingly popular tool to enable engineering teams to shift left. For example, engineers can train neural networks to search through enormous amounts of simulation models and data and help identify the ideal vehicle or component configuration.
Powered by AI, the effort to shift left is more urgent than ever as the world transitions to a more sustainable future with electrification. Many original equipment manufacturers (OEMs) are in the process of transitioning from producing internal combustion engines (ICEs) to battery-powered vehicles. Each of these vehicles has years of development data and simulation models that now need to be adapted for electrification.
Neural networks for vehicle target setting
The Hyundai Motor Group is a multinational firm headquartered in Seoul, South Korea. With about 250,000 employees worldwide, Hyundai Motor Group’s mobility brands include Hyundai, Kia and Genesis.
At the start of its electrification journey, Hyundai Motor Group (HMG) recognized the need to implement AI to enable a seamless shift left in the electric vehicle development process. In 2023, it partnered with Simcenter™ Engineering and Consulting services (Simcenter Engineering Services) to build the neural networks that will enable it to define architecture-driven requirements at the concept stage of vehicle development.
Early in the design process (at the left of the V-cycle), engineering teams typically have an estimate of what they would like to see in their next generation of vehicles including mass, size, suspension technology etc. These early ideas need to be explored and analysed in the most efficient way possible to define the ideal design and configuration. Target setting for attributes such as optimal mass; kinematics; drivability; ride and handling gives engineering teams subjective key performance indicators (KPIs) to meet. The earlier these targets can be met, the more time and cost savings a company can reap.
Ilsoo Jeong, comfort engineer, is part of the driving comfort virtual development team at Hyundai Motor Group. His team was tasked with target setting for chassis development of the Genesis GV 80, which will be released in a future generation as an electric vehicle (EV).
“Our goal was to achieve the best possible comfort and handling performance, so we had to consider hundreds of chassis parameters such as mass distribution, suspension kinematics and the mounting system,” said Jeong. “We also needed to consider how these designs and configurations would need to be changed considering the ICE will be replaced with a battery.
“Additionally, we wanted the ability to perform sensitivity analyses to quickly understand how changes to the design of one component may impact the performance of others. We realized that taking advantage of AI could help us accomplish this quickly and efficiently. We partnered with Simcenter Engineering and Consulting Services to build these neural networks because it had the most expertise in Simcenter Amesim, our preferred tool, and because of its vast expertise in the vehicle development process.”
EV architecture optimisation
In a separate project, the Simcenter Engineering Services team had collaborated with HMG engineers to develop an architecture in Simcenter Amesim™ software that could be used to evaluate a variety of vehicle manoeuvres and provide automatic post-processing. Simcenter and Simcenter Engineering Services are part of the Siemens Xcelerator business platform of software, hardware and services.
This architecture allowed criteria to be weighed separately, including 52 individual KPIs for each requirement, to achieve an overall score. It could handle input of over 350 parameters.
In this new project, Simcenter Engineering Services expanded on this work to apply it to the chassis. Using the targets provided by HMG, Simcenter engineers generated over 200,000 simulation models in Simcenter Amesim and validated them against real vehicles. They saved the simulation results in a high-performance computing (HPC) environment to make them run faster in the future.
To read the rest of this article in the November 2023/January 2024 issue of ISMR, see https://joom.ag/yond/p20