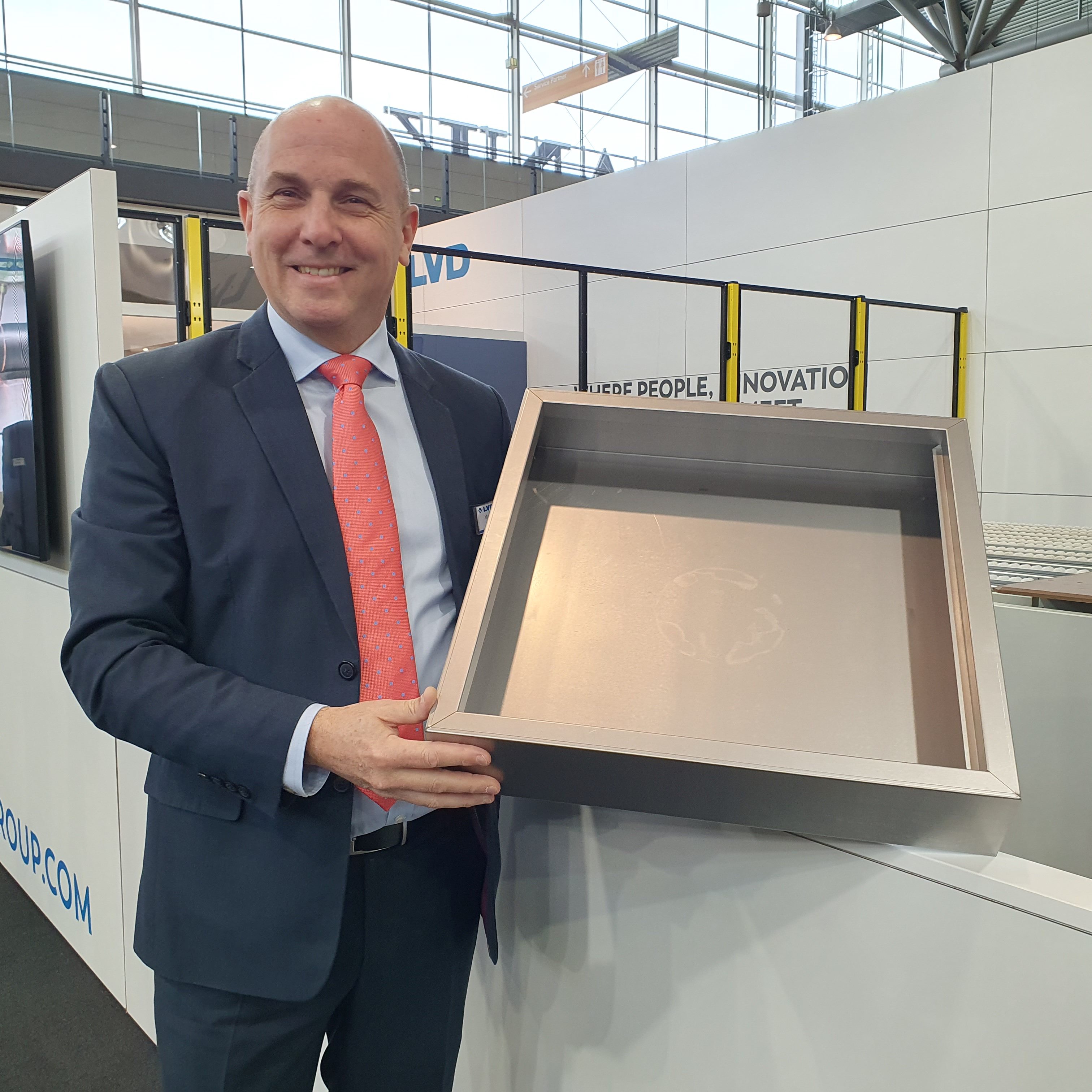
Feeding the flow
Submitted by:
Sara Waddington
Image caption: LVD’s Group Marketing Director, Matt Fowles, at Blechexpo/Schweisstec 2023.
At this November’s Blechexpo/Schweisstec trade show in Germany, LVD Group launched a new panel bending range as well as new laser cutting technology and software.
LVD is a leading manufacturer of sheetmetalworking equipment including laser cutting systems, punch presses, press brakes, guillotine shears and automation systems, integrated to and supported by its CADMAN® software suite. LVD Industry-4.0-ready products and technology are geared towards smart manufacturing.
With its global headquarters in Gullegem, Belgium, LVD Group operates production facilities in Belgium; the U.S.; Italy; Slovakia and China. It has dedicated offices, and over 1000 employees, as well as direct representation in 47 countries. The family-owned business has, for the sixth consecutive year, been named one of ‘Belgium’s Best Managed Companies’ by Deloitte Private, Econopolis and KU Leuven. The designation recognizes privately-owned Belgian firms that translate a clear strategy, strong capabilities and employee engagement into strong financial results.
At this November’s Blechexpo/Schweisstec trade show in Stuttgart, Germany, LVD Group introduced a host of new technology and software launches. ISMR caught up with LVD’s Group Marketing Director, Matt Fowles, on its booth at the exhibition to discuss these new developments and gauge his views on sheet metal market trends, processes and challenges.
Launch of panel bending range
A major news announcement at LVD’s booth was the addition of panel benders to its portfolio of flexible solutions for sheet metal processing. Its new product line offers a range of servo-driven, customisable panel bending equipment, including high-speed panel bending systems. LVD launched the new line at Blechexpo/Schweisstec with the unveiling of the PB 21/12 automatic panel bending machine (which it demonstrated to ISMR).
Panel bending technology can process large and complex geometries quickly and efficiently with high productivity in medium to high volumes. It is suitable for producing large electrical cabinets; panels and cabinet components; shelving; clean rooms; steel furniture; architectural building panels; photovoltaic components; trailer side panels; lighting as well as other industrial equipment panels featuring complex geometries with radius bends, short side lengths and narrow profiles.
LVD will initially offer three models of panel benders: PB 21/12, PB 25/12 and PB 32/12 to handle panel sizes of up to 3200mm x 1250mm. On its stand at Blechexpo/Schweisstec, it showcased an automated PB 21/12 system. The panel benders can be customised to expand capacity and performance. A universal set of folding blades enables the processing of a wide range of profiles and bends. Most profiles can be formed using a single set of tooling.
“We are very excited to introduce our panel bending technology to the marketplace. It has attracted huge interest here at the show and is a natural complement to the very wide range of press brakes that we make. The technology also fits well with our strategy of adding value to our customers’ businesses,” LVD’s Group Marketing Director, Matt Fowles, told ISMR at the exhibition.
“We see panel bending as a natural addition to our product range and the next step to offering a one-stop shop to our customers. Over the last few years, we have added more automation products for laser and punching, as well as more tube laser cutting. Customers want more throughput, handling and automation capability. We see panel bending as a natural progression, as some of the unique features of our panel bending technology fit with the way that users need to process material these days. A good example of this is offline referencing of the blank, rather than in-machine referencing, to keep throughput and process flow steady,” he added.
The automated PB 21/12 on LVD’s stand can process a panel of up to 2.1m long x 12.5m wide in up to 1.6mm material thickness. This model features a combination of automated loading, with semi-automatic offloading, in the demonstration shown to ISMR. The combination of multiple input stations gives users the flexibility to maintain throughput for a higher mix of parts. On the output station, an automatic out-feed from the bending zone enabled users to retrieve parts manually (also available as an automatic option) to illustrate the flexible and customised approach adopted by LVD.
Laser cutting and software
Another new addition at the Blechexpo/Schweisstec exhibition was LVD’s large-format Phoenix FL-6525 laser cutting machine with bevel cutting head, as well as new CADMAN®-FLOW software for optimised material process flow.
The new Phoenix FL-6525 offers versatility and capacity with a large cutting range up to 6510 x 2600mm and a bevel cutting option. Its large-format configuration is designed for cutting oversized sheets in thin to thick materials. The bevel cutting head provides precise control of the angle and depth of the bevel to cut intricate contours or for weld-prep operations.
Phoenix FL-6525 is available with 6-, 10-, 12- or 20kW laser power. The bevel-cutting option is available for 10- and 12kW systems. The Phoenix FL-6525 at Blechexpo/Schweisstec featured a 12kW laser source with bevel head.
To read the rest of this article, see https://joom.ag/ztnd/p20