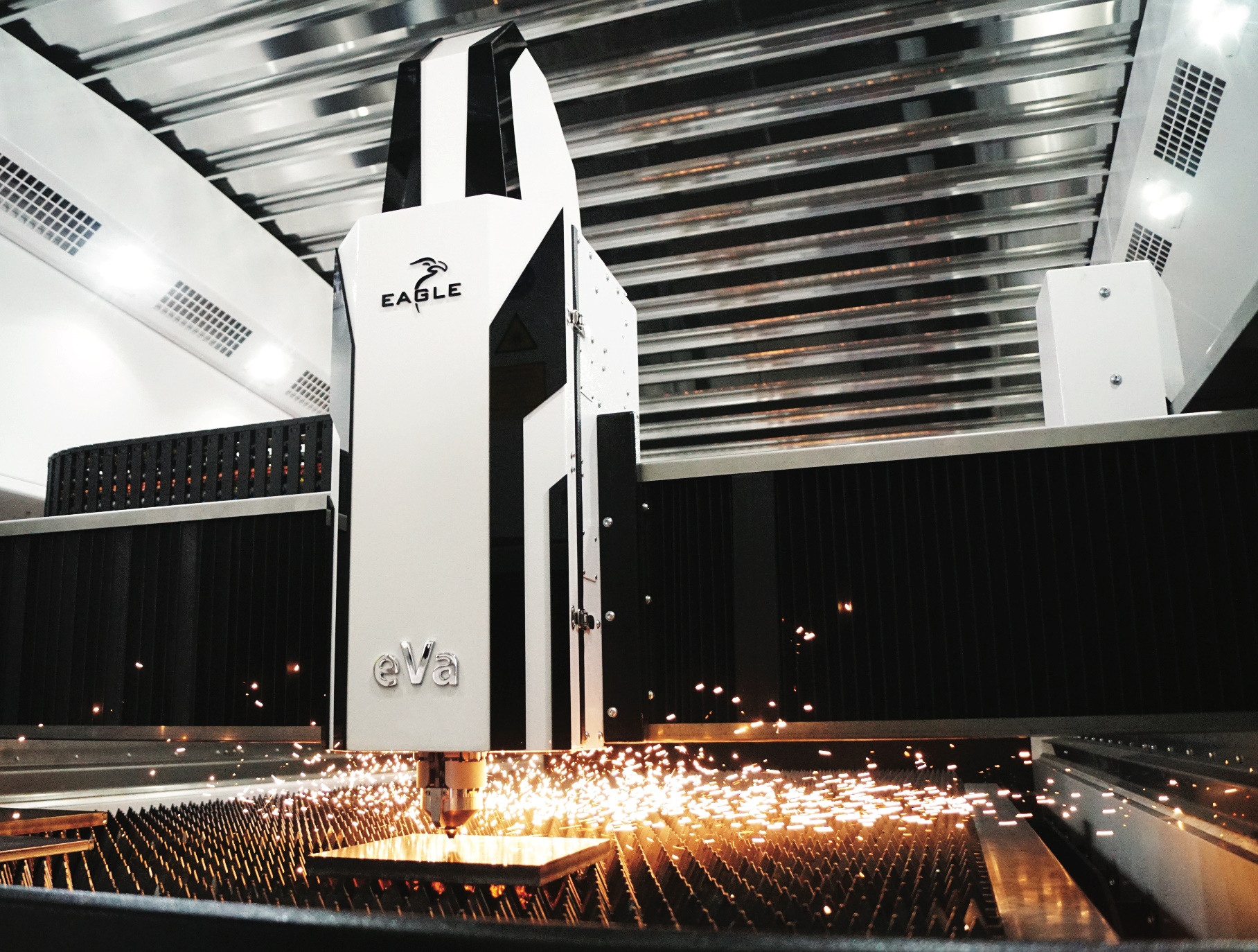
Focus on fibre
Submitted by:
Sara Waddington
A selection of the latest new fibre laser cutting innovations in the global market come under the spotlight in this article in ISMR’s March 2024 issue.
====
Laser cutting is a thermal cutting process for processing sheet metal. The laser beam is created by the laser source (resonator), conducted by a transport fibre or mirrors in the machine cutting head where a lens focuses it at very high power on a very small diameter. This focused laser beam meets the sheet metal and melts it. In addition to flat materials, tubes and profiles can also be processed by laser cutting systems.
Fibre lasers are a very efficient mode of laser cutting. The laser beam is created by an active fibre and transmitted over a transport fibre to the machine cutting head. A fibre cutting system is primarily suited for processing thin to thick sheet metal from steel, stainless steel, aluminium and also other non-ferrous metals (copper and brass). Other benefits include their high output power and very high optical gain, compared to other types of laser.
Depending upon the cutting technique employed, different process gases are used, and these are forced through the kerf at different pressures. The various techniques differ primarily in respect to cutting speed and the quality of the cutting edges. Examples include flame cutting, fusion cutting and cutting gas. Fibre laser cutters can also be comfortably used for the efficient processing of gauge and fractional materials, as well as fine feature cutting.
The fibre's waveguide properties reduce or eliminate thermal distortion of the optical path, typically producing a diffraction-limited, high-quality optical beam. Fibre lasers are compact compared to solid-state or gas lasers of comparable power, because the fibre can be bent and coiled (except for thicker rod-type designs) to save space. They exhibit high temperature and vibrational stability, as well as extended lifetime. The additional power and better beam quality provide clean cut edges and rapid cutting speeds.
In this article, we highlight a selection of the latest new fibre laser cutting innovations in the market today.
Fibre laser innovations
AMADA’s REGIUS fibre laser cutting machine integrates three-axis linear drive, AMADA’s original Variable Beam Control technology, new Laser Integration System (LIS) functions and easy operation. LIS functions include the i-Nozzle Checker, the i-Process Monitor and the i-Optics Sensor. Readiness for cutting is monitored during operation and automatically restored after collisions.
“Variable beam adjustment automatically and continuously matches energy distribution in the laser beam (not just focus diameter and focus position) to the material to be processed and its thickness. The mode can be adjusted as required during piercing and cutting, making it possible to run the piercing process at high speeds and with increased productivity,” AMADA explained.
Its VENTIS-AJ fibre laser cutting system features an innovative beam shaping system that allows for precise control of the laser beam motion. Utilizing AMADA’s high-power, single diode module fibre laser engines, the VENTIS is available as a 4kW or 6kW machine.
“These engines provide a very high-quality laser beam, allowing the 4kW VENTIS-AJ to perform similar to 6-8kW machines, and the 6kW VENTIS-AJ to perform similar to 8-10kW machines, with much less of a power requirement,” explained AMADA.
The ENSIS-AJ range is available with 3-, 6-, 9- and 12kW fibre laser engines developed by AMADA using 3- and 4kW diode modules. The 6kW, 9kW and 12kW versions utilise AMADA’s Auto Collimation system for laser beam spot control. Combined with AMADA's original Variable Beam Control technology to adjust the laser mode, this system can process different materials and thicknesses with a single cutting lens.
The fibre laser tube cutting machine, ENSIS-RI, can process round, square and rectangular tubes as well as channel and angle profiles.
“ENSIS technology for laser beam control and the Rotary Index system for tube cutting are combined in a machine that can deliver on an extensive range of production requirements,” confirmed AMADA.
AMADA’s LC-ALPHA V is suitable for processing surface sensitive materials and is a hybrid laser machine. The new LC-αV NT range has been designed to make sheet metal loading particularly easy. The new AMADA-tuned 3.5 kW oscillator utilised in the LC ALPHA V NT has been designed with a higher beam density for the processing of thin to mid-thickness materials. This offers a reported 30% improvement in beam density (compared to a conventional machine).
AMADA set up the new AMADA Global Innovation Centre (AGIC) in Japan last year which it is also using to introduce new technologies, software and machine tools to its customers. Demonstrations on the 12kW REGIUS 3015 AJe fibre laser cutting machine at Innovation Site 01 included AMADA’s new cutting innovations such as the fibre silky cut improvements on aluminium and stainless steel. The technique involves a mixture of optical path (beam) adjustments, higher power fibre engines and gas flow dynamics and is an automatic function of the machine once the operator selects the cut data.
New AMADA LBC Flash Cut technology is also demonstrated on a 6kW VENTIS 3015 AJe laser cutting system. AMADA has developed a way of cutting holes without moving the cutting head but by manipulating the beam, a huge time-saver for manufacturers who do a lot of perforated part cutting or cut thousands of small holes in sheet metal.
Turkish manufacturer, Baykal Machinery, has developed its fibre laser cutting systems for robust continuous operation as well as accuracy, efficiency and speed. Since its first step into this area in 2007, Baykal has now become a major manufacturer of fibre laser cutting systems in Turkey.
At Blechexpo in Stuttgart (November 2023), Baykal promoted its BLC 25m-long combination fibre laser, which combines both tube and sheet metal processes together into one single machine. Since it eliminates the time required to transfer workpieces between different machines, the BLC is designed to enhance productivity.
Its BLE small fibre laser cutting system (1-3kW) features an auto-focus cutting head. The BLE Pro Tower is a fibre laser cutting system (1-6kW) with a Compact Tower loading and unloading device for 1500-3000mm maximum sheet size (maximum sheet thickness of 16mm) and rapid traverse speed of 110m/minute.
Its BLS Series fibre laser cutting systems cover a wide range of industrial applications. Manufactured with an “All-in-One Box” design structure, the BLS has a built-in resonator and a chiller with dual motorised tables. A range of fibre power sources are available. The BLS uses a new generation, high-performance linear axis system with rack and pinion. The BLS Pro series features power sources from 6-20kW.
“With fibre laser technology, there is no need to move the laser source or sheet, enabling high-speed, accurate cutting and dual full-size pallet maximum production throughput. Machines have a simple and user-friendly operator interface, as well as an extensive cutting database,” the company told ISMR.
Boschert GmbH & Co KG celebrated its 75th anniversary in 2021. Based in Lörrach (near Freiburg, Germany), Boschert employs 120 members of staff and has a production and assembly area of some 8,000 square metres. Its FiberLaser 3015 and 4020 systems offer speeds of 100m/minute and laser power of up to 4KW.
The trend in manufacturing is to make components that are lighter in weight, use less material, conserve resources and integrate functionality (i.e. thinner sheet structures). Boschert has expanded its “Combi” series of machines to include fibre laser. Now, users can produce complex parts on a single machine without repositioning. The Boschert CombiLaser combines the advantages of laser cutting with the unique features of CNC punching. Boschert’s fibre laser system can be mounted to any of Boschert‘s standard line of CNC punching machines.
Swiss manufacturer Bystronic’s new ByCut Star 3015 cuts sheet metal with measurements of 3 x 1.5m is available with power of up to 30 kilowatts. The latest smart features include the “Intelligent Cutting Process (ICP),” the “Nozzle Control Tool (NCT) with KerfScan” and the “Parameter Wizard”. Its ByCut Star 4020 offers the same high laser power but for larger sheet metal sizes.
“Cutting thicknesses of up to 50mm become reality. The cutting speeds of the ByCut Star therefore increase significantly compared to 15kW and MixGas for sheet thicknesses of between 6mm and 15mm. The piercing times are also shorter for sheet thicknesses from 15mm,” commented Bystronic.
With its new laser output of 20 kilowatts, Bystronic’s ByStar Fiber cuts steel, aluminium, stainless steel, brass and copper. The new power level is available for the ByStar Fiber 3015, the ByStar Fiber 4020 and the extra-large format ByStar Fiber 6225 and ByStar Fiber 8025. The 20kW output enables advanced applications in steel and aluminium of up to 50mm. Using a 21.5-inch touch screen, Bystronic’s BySoft Cell Control Cut software is operated “as simply as a smartphone”, the manufacturer told ISMR.
Bystronic’s ByCut Smart range includes the ByCut Smart 3015 (small model with new laser power of up to 15kW); the ByCut Smart 6225 (which can process larger sheets) and the ByCut Smart 12025. With the XXL fibre laser cutting system and a laser power of up to 15kW, users can process sheets of up to 40.02 x 8.20 feet on the ByCut Smart 12025. The 6kW ByCut Eco 3015/4020 offers users an entry-level step into laser cutting sheet metal.
The compact BySmart Fiber offers strong cutting performance with up to 12 kilowatts of laser power. It can be expanded with additional functions such as an automatic nozzle changer; the "BeamShaper" to help the laser cutter process metal of up to 30mm; the "Parameter Wizard" and the "Detection Eye" function (to rapidly determine the position of the sheet on the cutting table).
Bystronic’s fibre laser tube cutting systems include the 4kW ByTube Star 130 with Quick Cut functionality and the FL 170 3D tube laser cutting machine. The company also offers a range of automation options for its sheet and tube laser cutting systems.
To read the rest of this article in ISMR’s March 2024 issue, see https://joom.ag/ZkAd/p50