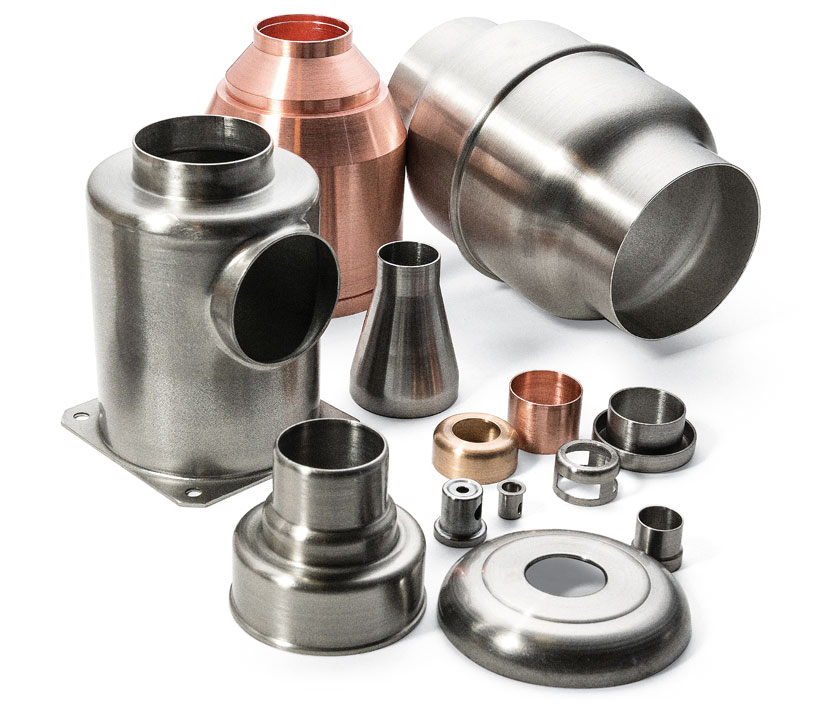
Forming the future
Submitted by:
Sara Waddington
Deep drawing is a manufacturing process in which sheet metal is progressively formed into a three-dimensional shape through the mechanical action of a die forming the metal around a punch. The deep drawn metal stamping process work hardens the metal, resulting in a seamless finished part that is stronger than the base material. When the length of a stamped part is equal to or greater than ½ of its diameter, it is generally termed as being "deep drawn."
Deep drawing uses radial tension-tangential compression to shape the metal. This deep drawn process transforms flat sheet metal, or a blank, into a hollow vessel that may be cylindrical or box-shaped, with straight or tapered sides or a combination of straight, tapered and curved sides. The vessel is then redrawn through a series of dies, reducing its diameter and increasing its length with minimal change to the wall thickness. A flat sheet metal blank can be formed into a hollow body open on one side or a hollow body can be formed into a hollow body with a smaller cross-section [DIN 8584].
Deep drawing is one of the most widely used processes in sheet metal forming. Apart from its use in many other sectors, it is applied in the automotive industry for the manufacturing of car body parts. Deep drawing can produce precise and intricate parts, including both symmetrical and asymmetrical parts. Many different metals, such as cold rolled steel, stainless steel, titanium, copper, brass, aluminium, HSLA and others, are included in the deep drawn metal stamping process.
Seamless sheet metal parts
Deep drawing creates seamless, sheet metal parts that are closed at one end and have a depth greater than their radius. Deep drawn parts achieve their shape by drawing metal into a cavity rather than by stretching or thinning over a die, so the original sheet thickness remains essentially the same from start to finish. A deep drawn part can be recognized by its depth and smooth, radiused corners. Examples range from cans, pots, kegs and compressed gas cylinders to eyelets, sinks and automotive body panels.
“Simple parts can be drawn to their finished shape in a single step while complex shapes, including parts that are especially deep, may require multiple steps. Deep drawing typically is used in combination with other techniques, such as blanking and piercing, to create a finished product. In some cases, all steps can be completed using a single press,” commented press manufacturer, Macrodyne.
“Deep drawing works best with ductile metals. In general, any metal that can be cold rolled into sheet should have sufficient ductility to be deep drawn, but material properties like work hardening or anisotropy also may need to be considered. Appropriate materials include aluminium alloys; brass, copper and copper alloys; titanium; cold rolled low carbon sheet steel and some stainless steels. Ideal shapes for deep drawing include rectangles and axi-symmetric structures such as cylinders or hemispheres, but the process can also handle more complex shapes,” it continued.
Depending upon the shape being produced, tooling and setup costs can vary widely. For simple shapes, costs can be lower than other processes, but with increased complexity comes increased cost. In some cases, that cost may be offset by deep drawing’s minimal downtime, low maintenance, and reduced technical labour requirements over the lifetime of the product.
Stamping characteristics
The deep drawing process contains many components and steps. All of these deep drawn processes combine to influence the metal stamping industry. There are various characteristics of deep drawn stampings/pressings, which can be summarised as follows:-
To read the rest of this article in the June 2024 issue of ISMR, please see https://joom.ag/UVkd/p42