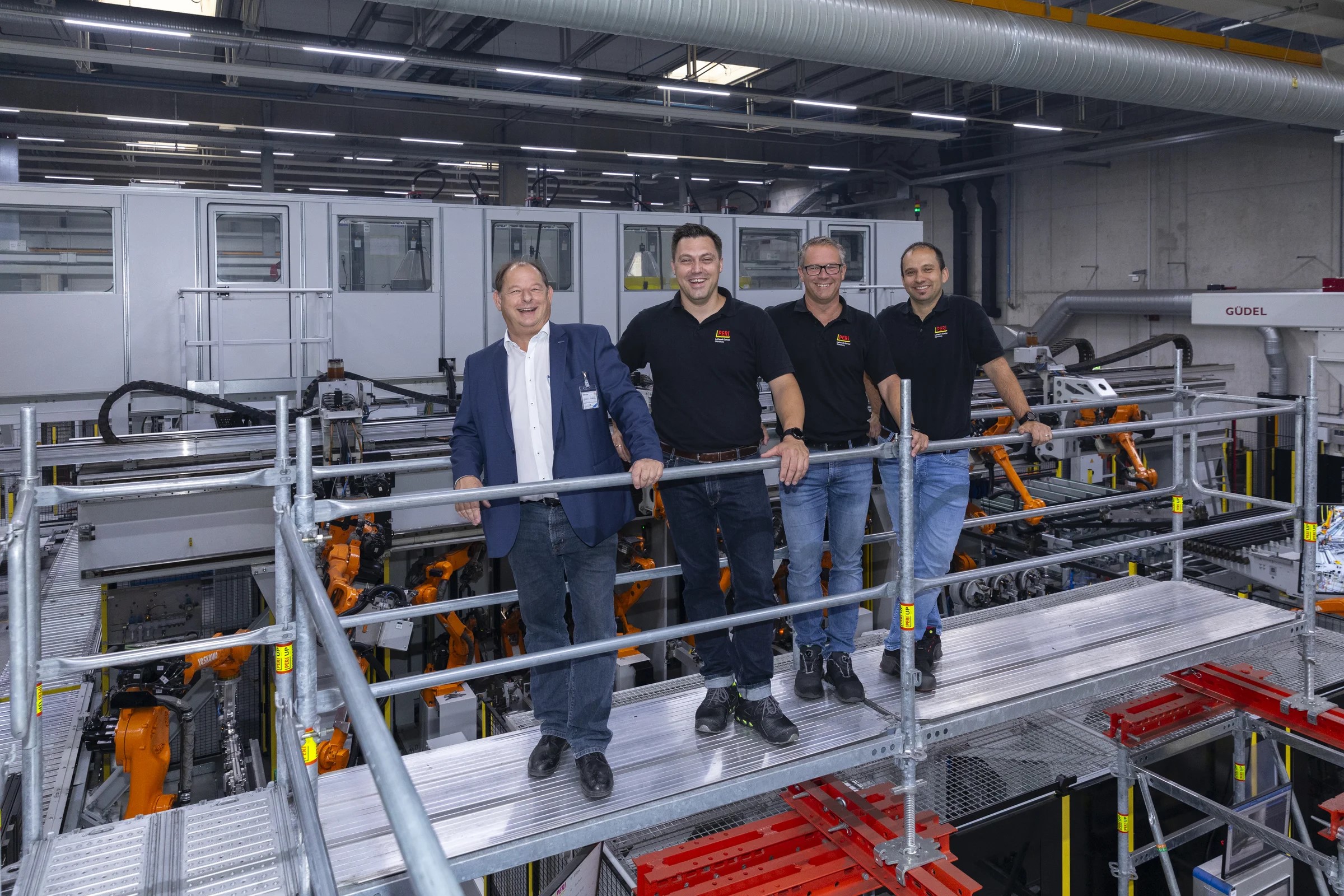
Handling and welding
Submitted by:
Sara Waddington
In the February 2024 issue of ISMR, we outline how Yaskawa’s robot specialists were able to solve the tasks involved in commissioning a new horizontal ledger welding system at PERI’s new scaffolding ‘master plant’ in Günzburg, Bavaria.
=====
With a pioneering technical spirit, family-owned company PERI supports construction companies, scaffolding contractors and architects with innovative formwork and scaffolding solutions for the new construction, conversion or renovation of buildings and structures. Tailor-made logistics, service and engineering services complete the portfolio.
In existence for over 50 years, PERI has become one of the leading manufacturers and suppliers of formwork and scaffolding systems as well as 3D construction printing supplies. Headquartered in Weißenhorn, Germany, the group employs over 2,000 engineers in more than 70 countries. In 2016, PERI acquired a new site including production halls and office buildings in Günzburg, Bavaria, around 20km away. It also has a plant in Sakaya, Turkey. These have significantly increased its production capacities.
The PERI UP Scaffolding Kit combines the advantages of frame and modular scaffolding in one integral construction kit. Around 500 system components are compatible with each other and can be combined in a flexible manner. With just one scaffolding system, facade, industrial and engineering scaffolders can cover most modern scaffolding applications.
High levels of automation
The production process also reflects the company’s high standards. Modern processes and a high level of automation throughout the company lay the foundations for high levels of quality and efficiency from the start. Recently, the company built its new “scaffolding master plant” in Günzburg, Bavaria-Swabia (Germany), and bundled the complete production for PERI UP scaffolding technology at this site.
Since 2016, more than one hundred Motoman robots from Yaskawa have been in use at the plant.
“At the PERI plant in Weissenhorn, we have been using many of our Yaskawa robots successfully and consistently for more than 30 years. And yet, before setting up the new production facility, we took one last critical look at our robotic set-up,” explained Stephan Schraml, Head of the Technology Centre at the PERI plant in Günzburg. “It was confirmed; our robotics requirements are best met by Yaskawa quality.”
Fully automated ledger welding system
A further 18 new Yaskawa robots were recently added to a fully automated handling and welding system at PERI. Their task is the fully automatic production of ledgers, which are used hundreds of thousands of times in scaffold construction. The ledgers are complex to produce due to their integrated self-locking mechanism and the square design. Movable wedges ensure convenient and safe assembly. At the same time, they place high demands on the production technology.
“Even if you can’t see it, due to the integrated wedges, the design of the components allows only very small tolerances. They must therefore be manufactured with precision,” confirmed Stephan Schraml.
Also referred to as runners, ledgers are tubes that run horizontally along the length of the scaffold. This component is used to support the working platform of the scaffold. Based on its placement, it determines the height at which the working planks (decks, boards etc.) are staged.
Previously, production at PERI was partially automated using half a dozen robotic welding systems with a rotary table and manual feed.
“This also worked,” recalled Schraml, “but with significantly longer cycle times, more logistical effort and less flexibility with regard to the size of the components.”
The new ledger welding system now handles the entire manufacturing process, from the individual blanks to the finished component. This includes 100% monitoring of welding parameters, optical seam inspection using cameras, and length and angle measurement. Final palletising for onward transport is fully automated, as is the entire system operation. Only one operator per shift is required to monitor the processes.
By using multiple welding stations in parallel, the system can produce more than one thousand ledgers per shift. The plant was designed to PERI’s specifications with optimum use of space. The very complex, space-optimised design is only possible by implementing a wide variety of robot arrangements, such as the use of gantry systems.
To read the rest of this article, please see https://joom.ag/HU0d/p44