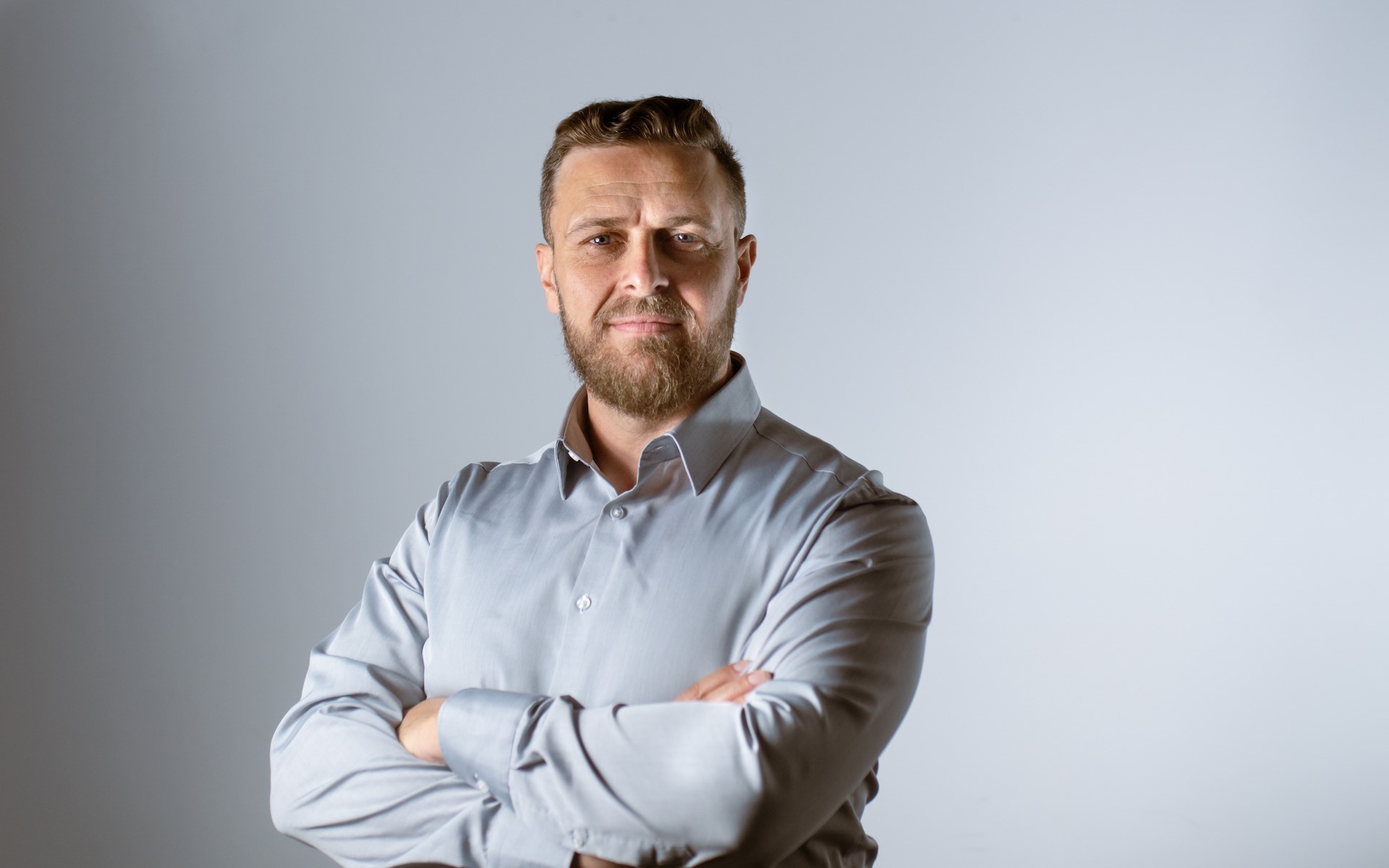
The ‘high fives’ of fibre laser
Submitted by:
Sara Waddington
(Image: Camillo Brena, Marketing Director, Eagle Lasers.)
Eagle Lasers outlines the five main aspects to consider when evaluating fibre laser technology in 2023.
================
In today's industrial landscape, where efficiency and productivity are paramount, fibre laser technology has emerged as a game-changer. Its widespread adoption is fuelled by technological advances; enhanced reliability; reduced space requirements; simplified operation and lower energy consumption compared to its predecessors.
Undoubtedly, companies that embrace fibre laser technology stand to gain significant advantages. However, making an informed decision about adopting a fibre laser cutting system in 2023 requires the careful consideration of several key aspects. These considerations are not limited to specific industries and can be applied broadly to all metal cutting companies.
In this article, Eagle Lasers explores the five main aspects to consider when evaluating fibre laser systems before making a purchase.
High performance
“The first aspect to consider is high performance,” said Camillo Brena, Marketing Director, Eagle Lasers. “The interplay between laser power, motion dynamics and automation is pivotal for achieving the best productivity and efficiency in laser-based applications. It is only through their collaborative action that we will achieve highly sought-after peak performance.”
The laser industry is currently experiencing a remarkable surge in power levels, with machines now capable of outputting up to 40 kilowatts (kW) of laser power. This exponential increase is expected to continue escalating in the foreseeable future. Traditionally, material thickness has served as a reliable indicator of the required laser power; the thicker the material, the more power needed to cut through it effectively. However, the landscape has evolved beyond this simplistic metric.
“While the allure of these impressive power figures remains undeniable, it is essential to recognize that ‘brute force’ alone is not enough. Without precise control and proper application, it could yield counter-productive results,” continued Brena.
The integration of power with dynamics, precision and automation is the key to unlocking the full potential of laser technology. For instance, investing in a high-wattage laser machine without addressing its motion dynamics can lead to sub-optimal productivity.
According to Brena: “A laser system must be capable of precise and rapid movements to fully exploit its power potential. Conversely, a machine with remarkable speed but a slow material exchange process will waste that speed and won’t reach its maximum productivity.”
With the pressure to deliver orders faster, better and at a lower cost, manufacturers must consider a broader spectrum of factors including production volume, growth rate and market demands. Due to the increasingly varied nature of order types and sizes, adaptability is gaining considerable importance and is seen as an investment in future competitiveness as it allows manufacturers to cater to diverse customer needs and market trends.
High usability
“The second aspect to explore is high usability,” continued Brena. “Usability is a critical aspect that must not be overlooked when considering the adoption of laser technology, particularly in the context of high-power machines where maintaining control and precision is even more relevant.”
The usability factor is of special importance in manufacturing, where the implementation of new machinery can be a daunting challenge for operators. Managing a high-end laser requires a high level of skill, knowledge and experience. Hiring and training operators capable of efficiently working with these systems can be a challenge, especially within the prevailing labour shortage environment. In this scenario, manufacturers should not underestimate the relevance of ease of use.
High usability is as much about implementing features that make machine operation more accessible as it is about eliminating all unnecessary steps that complicate the process. An intuitive design has the power to bridge the gap between skilled operators and those who are less experienced. This ‘democratisation’ will empower a broader workforce to operate effectively.
As Brena put it: “Whether it's our smartphones, cars or kitchen appliances, today usability has taken centre stage in design and functionality. A laser cutting machine is no different. A good user experience in our field means interface user-friendliness; level of control; error prevention systems and quick access and visualisation of data such as files and reports.”
Additionally, users should consider mechanical but highly valued elements such as ergonomics, internal parts accessibility, a clear field of vision between the cutting bed and panel, among others. These resources not only make it easier for operators to harness the full potential of high-performing machines but also contribute to increased productivity, reduced downtime and overall efficiency.
High reliability
While laser equipment, power, speed and ease of use may be easy-to-spot attributes, their effectiveness can be compromised if frequent errors and maintenance requirements halt the machine. This is why high reliability cannot be overemphasized.
“Think of high-performing fibre laser cutting systems as Formula 1 cars,” said Brena, highlighting the analogy. “Every component is meticulously considered to deliver peak performance, from design to maintenance. Attempting to graft a high-performance engine onto an ordinary car is possible but leads to unreliability.
“Similarly,” he continued, “in fibre laser technology, high power and advanced features will only shine within a well-structured and reliable system which will depend on both the machine’s quality and its conception. Like a tailor-made suit versus an off-the-rack garment, proprietary components (thoroughly tested in-house) offer unmatched reliability compared to third-party components. In today's automated, precision-focused manufacturing landscape, reliability is no longer a luxury but a requirement.”
High productivity
When the first three "highs" have been successfully addressed, the outcome is a state of high productivity. A truly productive system involves a harmonious interaction of various players and components.
However, productivity does not solely rest on machine speed. While this factor is vital, it won't achieve the full potential of a system by itself.
In the quest for productivity, multiple factors come into play. A fast machine calls for automation systems that can keep pace with it and ensure its continuous operation, even during night shifts and weekends. Software also plays a pivotal role in boosting speed and efficiency while helping to save energy and consumables. Well-developed software should optimise cutting processes, minimize waste and streamline operations.
To read the rest of this article in ISMR’s October 2023 issue, see https://joom.ag/36gd/p54