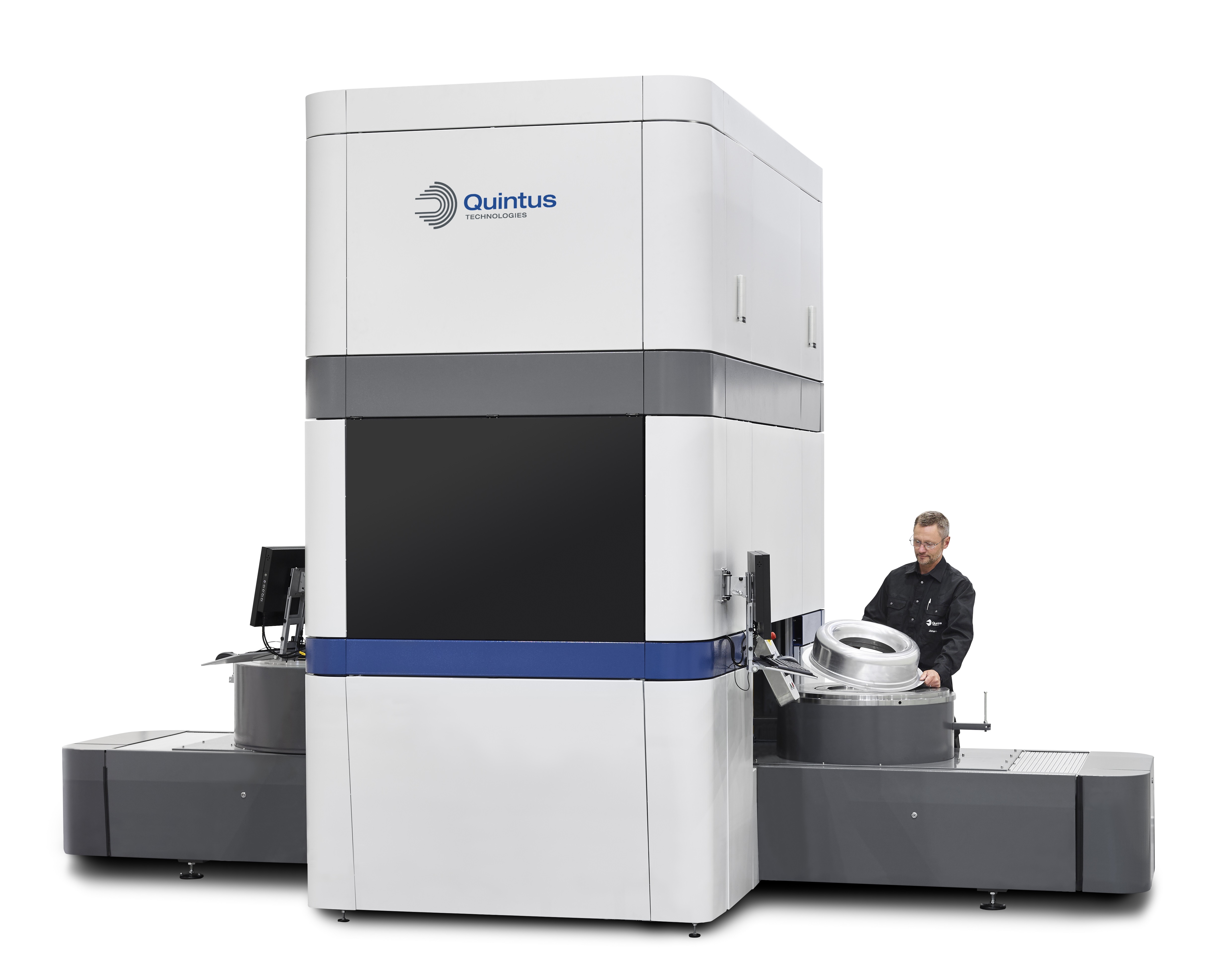
New deep draw press for Aeroforma Technologies
Submitted by:
Sara Waddington
The addition of a new hydroform deep draw press from Quintus Technologies brings increased capacity, flexibility and production efficiencies to aerospace parts manufacturer, Aeroforma Technologies.
Installed in the Aeroforma Technologies facility in Cheltenham, United Kingdom, the Quintus model QFM 1.1-800 Deep Draw Press uses hydraulic pressure up to 11,600psi to form parts in a variety of shapes, thicknesses and tough materials, achieving tight tolerances with minimal thinning. Proprietary flexible forming technology enables the press to perform four forming operations in a single machine. In addition to block tool forming, cavity tool forming and expansion forming, the Quintus press is also equipped with a movable punch forming system for the deep drawing of intricate shapes.
Aeroforma Technologies is a supplier of fabricated metal components to the aerospace industry. Installation of the QFM 1.1-800 represents 'its commitment to customers by bringing core processes under one roof to reduce lead times, streamline logistics and increase competitiveness'.
“Our strategy of providing a vertically integrated sourcing solution—from raw material procurement through to forming, welding, surface treatment and assembly—is one which our customer base is finding increasingly attractive,” said Antoni Kwiatkowski, Group Managing Director, Aeroforma Technologies. “Key to that strategy is ensuring the latest machinery, along with extensive industry knowledge and experience. With its hydroforming envelope and depth of draw, the Quintus press helps ensure that we remain ahead of the pack.”
The Quintus Flexform™ process utilises a combination of a single rigid tool half, operating in conjunction with a flexible rubber diaphragm subjected to high hydraulic pressure, to form sheet metal parts with accuracy and repeatability. This process produces high-quality parts, in complex shapes and tough alloys, and at tight tolerances. It is also designed to generate significant tool and process cost savings, of great value where intricately shaped components are required in low to moderate volumes.
The QFM 1.1-800 is equipped with two forming stations, one of which is the deep draw, offering a maximum blank diameter of 43.1 inches (1095mm) and maximum draw depth of 10 inches (254mm). The second forming station is tailor-made to accommodate block tool, cavity tool and expansion tool forming.
“Our Flexform technology is ideal for aerospace engine components, including deep drawn parts, in high-strength, heat-resistant materials,” said Jan Söderström, CEO of Quintus Technologies.
Aeroforma Technologies has supplemented its press purchase with a long-term Quintus® Care Programme for press operation and equipment maintenance.