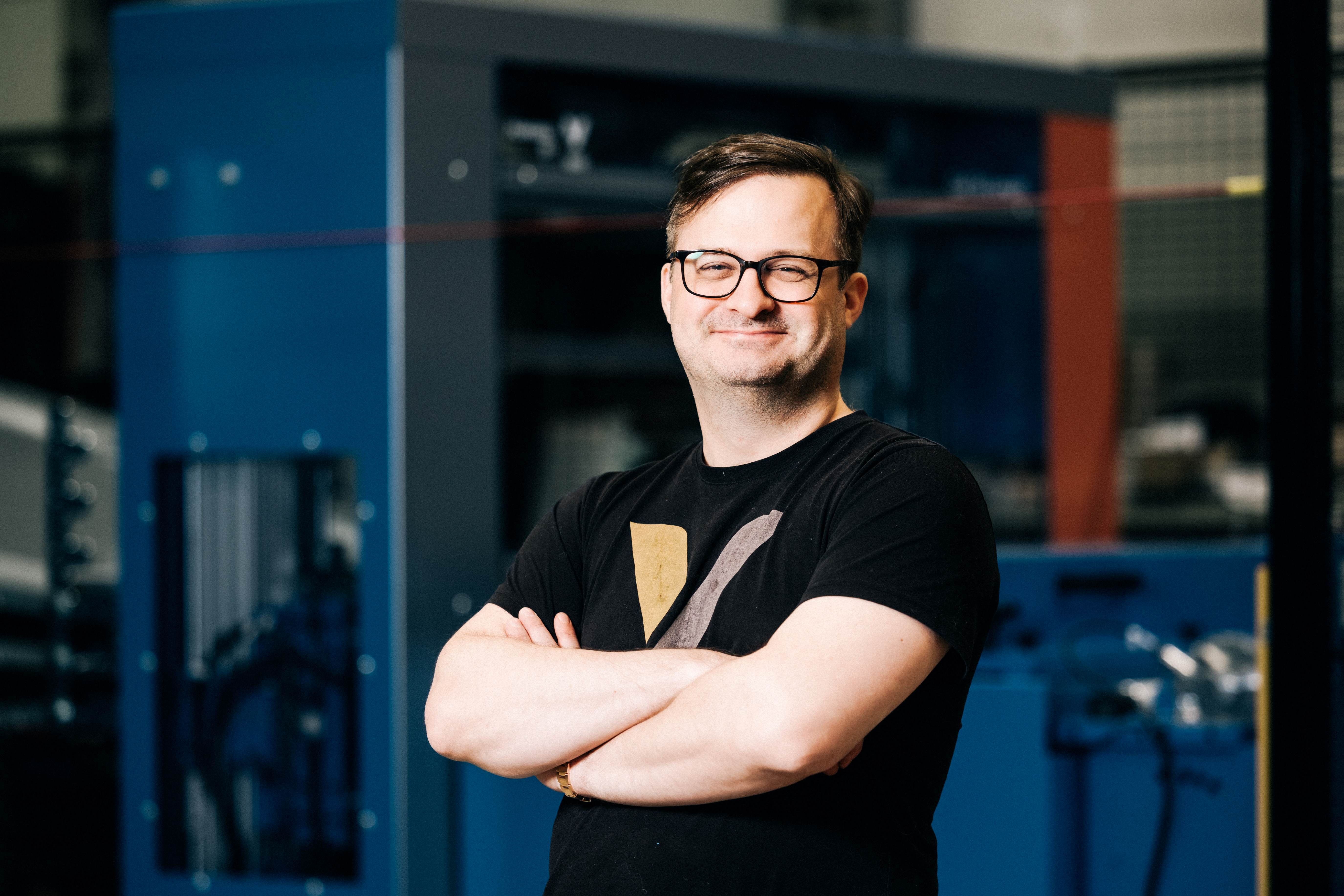
Productivity in focus
Submitted by:
Sara Waddington
Vaski Group Oy’s owner and managing director, Michael Mansour, outlines his expectations for the recent acquisition of Pivatic Oy and his views on global markets, new technologies and industry trends for manufacturers.
Vaski Group Oy from Seinäjoki, Finland, recently expanded through the acquisition of Pivatic Oy (Hyvinkää, Finland), a coil- and blank-fed punching and bending specialist. This marks a significant milestone for Vaski as it continues to strengthen its growth and position in the industry. Both Vaski and Pivatic have solidified their positions as international organisations with over 90% of products exported.
This combination is “a merger of equals, where both businesses individually achieved a record recent order backlog of €11 million,” Vaski’s owner and managing director, Michael Mansour, told ISMR. He sat down with ISMR to outline his hopes and expectations for the new acquisition, as well as his views of global markets, new technologies and industry trends for sheet metal and coil manufacturers.
ISMR: Please give a brief background to VASKI and highlight any notable successes and achievements over the past two years.
MM: I moved to Finland in 2020 when I took over management of Vaski Group Oy. I found a small Swiss company, HWJ, that made MULTICOIL blanking systems. It had very interesting ideas and technology, so I bought the business and drawings, focused the flat bar business, re-launched some next-gen products and started marketing them I then picked up lots of good engineers and technicians. Vaski’s business has grown well and it now, combined with Pivatic, has a €27m business with a strong machine order book.
Vaski offers custom machines but the standard machine business is growing very strongly at the moment. Vaski serves the sheet metal industry with its niche MULTICOIL blanking and slitting technology.
Our major USP is rapid and fully automatic coil changeover (in up to 40 secs). Operators have the flexibility of punching from blanks with the speed and material utilisation/nesting savings of working from coil. This is better for the circular economy and it means that the middle man can be cut out on blanking. Scrap is also lower with material savings from nesting. So, we have turned coil-fed punching into a flexible process.
ISMR: You bought Pivatic Oy earlier this year. Please take us through your reasons for this acquisition and the synergies that are involved?
MM: The Pivatic industrial fit is very strong for Vaski. Pivatic is a 50-year-old company with a large installed base and lots of service business. It makes well respected coil-fed punching systems (the company is number one in the world for coil-fed punching). It also manufactures wonderful niche punching and bending technology, which is why I bought the business.
Pivatic technology is great for applications that no-one else can do or if customers need an extremely high takt time. For example, some Pivatic machines are designed to manufacture electrical cabinets which are punched, bent and stud welded every ten seconds on a high-productivity line for one customer. That is an extremely rapid, continuous working time with the sheet moving efficiently through the line and being processed into hundreds of parts. Now, using Vaski MULTICOIL technology, the line only stops for less than 40 seconds for automatic coil or material changeover. This keeps productivity high so the combination of Vaski and Pivatic technologies works very well.
Both Vaski and Pivatic are based in Finland and have the same supply chain; CNC suppliers; tooling; laser marking etc. In my view, there is no company with a closer industrial fit (in terms of how machines are designed and built) for us than Pivatic. Our products are complementary: we both make highly customised machines and tailored solutions for customers so there was a logic to the choice.
Vaski significantly enhances its coil-fed systems business with Pivatic’s focus on coil-fed punching and bending lines for sheet metal processing. Pivatic, in turn, benefits from Vaski’s focus on coil-feeding technologies for industry.
ISMR: How is the Pivatic integration going? How will you manage the businesses going forward?
MM: I love the Pivatic brand. It might be that we move the coil feeding systems under the Pivatic brand in the future. However, Vaski also ‘coil enables’ various machine builders today so we will probably retain the Vaski brand when selling to machine builders and, when selling to end customers, do that through Pivatic. There will be some sales integration but I am separating direct customers sales from partner sales and sales support. There must be no crossover.
We will also probably sell the blanking and slitting solutions through the Pivatic brand to end customers—these fit very nicely as a sheet metal solution and complement our customers’ activities. Vaski will keep supplying flat bar solutions: 80% of its business is in the copper market i.e. switchgears; transformers; charging station infrastructure; power generation and data centres
ISMR: What are your hopes and expectations for this acquisition?
To read the rest of this article in the October 2024 issue of ISMR, please see https://joom.ag/LHud/p46