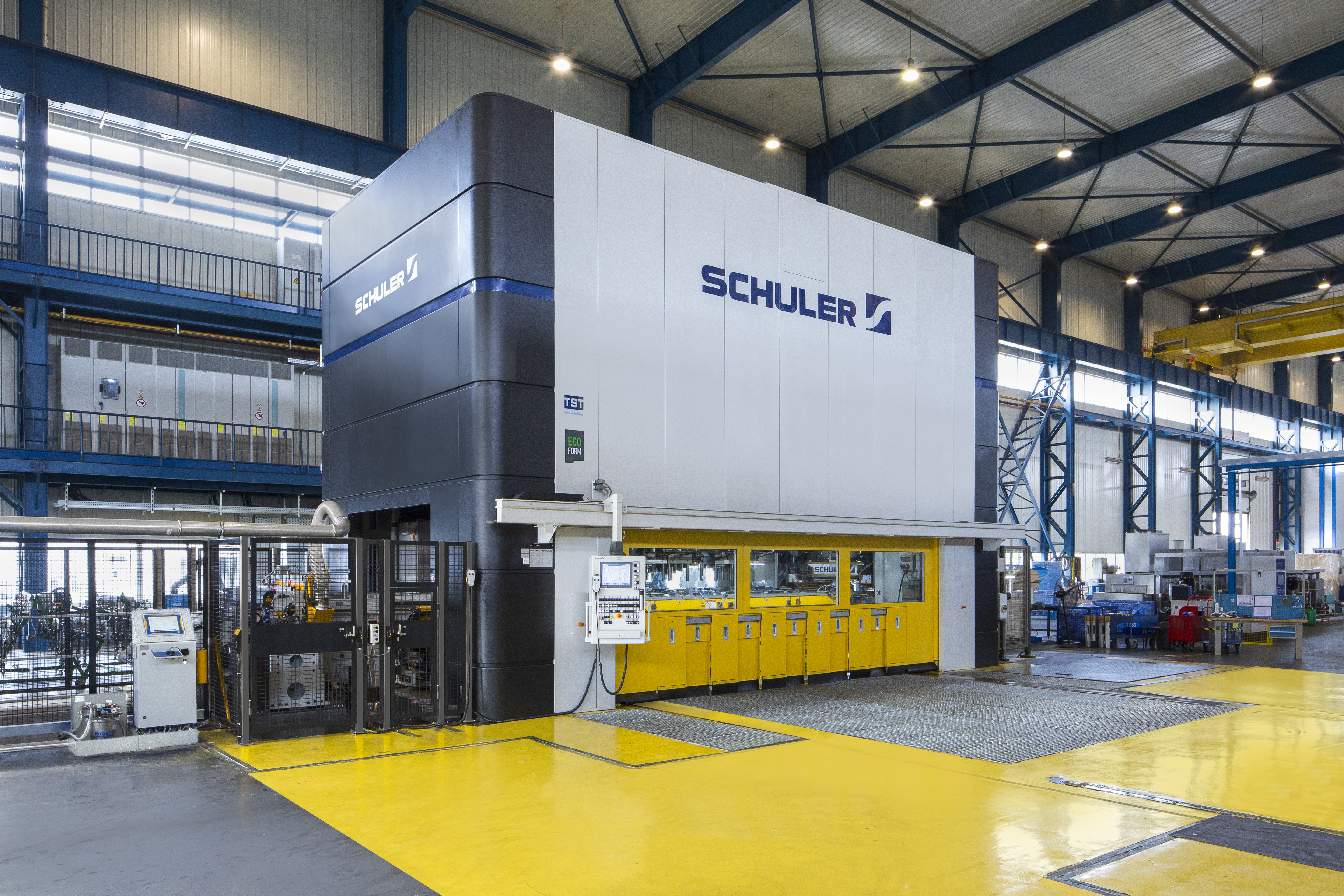
Schuler delivers TwinServo press to V-ZUG AG
Submitted by:
Sara Waddington
Header image: Swiss household appliance manufacturer, V-ZUG AG, has ordered a 1,000-ton TwinServo press from Schuler.
As part of a comprehensive consulting contract, Schuler analysed the press shop of Swiss-based V-ZUG AG. The recommendation to increase productivity was an investment in a 1,000 metric ton press with TwinServo technology. V-ZUG AG ordered the system at the end of 2017 and Schuler is now delivering the order to its facility in Zug in Switzerland. Start of production is scheduled for the end of September 2019.
Roland Häfliger, Project Manager, V-ZUG AG, describes the TST presses as a “milestone in terms of quality and performance”.
“They are precisely programmable, flexible and efficient. Thanks to the servo drive, we reduce energy consumption and can produce resource-efficiently,” he told ISMR. With the investment, V-ZUG AG expects to remain “marketable and competitive”.
“Presses with TwinServo technology are driven by two separate torque motors in the press bed. The electronically synchronised drives are arranged in such a way that there is still plenty of room for the scrap chutes. High tilt resistance, combined with reduction in deflection, leads to an improvement in the quality of the parts, reduces stresses on the die and shortens the die tryout times,” explained press specialist, Schuler.
Up until now, all sheet metal parts for V-ZUG AG products – such as washing machines, dryers, ovens, steamer and dishwashers – have been produced on hydraulic presses. Its declared goal now is to gradually transfer the production to the servo press.
“The coil line is designed in such a way that the machine can process all kinds of sheet,” explained Häfliger, “from galvanized sheet steel to the mirror-smooth chrome steel surface.”
Acting on Schuler's advice, changing dies (with a weight of up to 32 metric tons and a size of 6 x 2 metres, which automatically move from the warehouse to the press) is reduced to less than 15 minutes.
“Our employees are trained to handle every move,” said the project manager. “That allows us to produce even the smallest batch sizes.”
V-ZUG AG attaches particular importance to the fact that the machines – in which approximately ten km of cable are laid – are prepared for the requirements of Industry 4.0. For this reason, Schuler not only used the latest bus systems and decentralised installation techniques, but also IO-Link-capable sensors. This means that the setting data of the sensors are programmed in the control and can therefore be exchanged without having to be readjusted by the service personnel.
Subscribe to International Sheet Metal Review to receive 10 magazines per year, packed with the very latest industry news and product reviews.