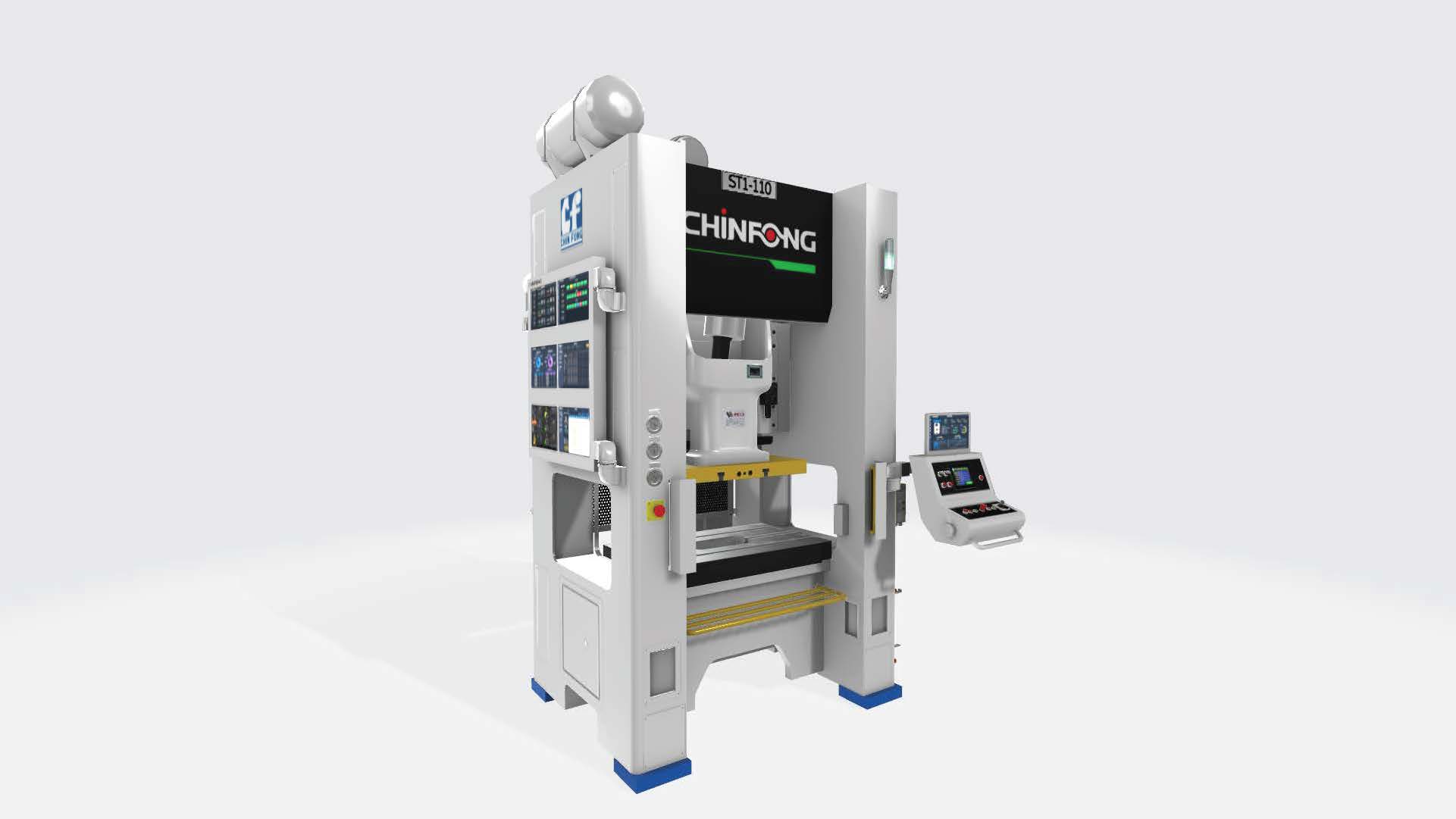
Chin Fong - Smart Stamping Solutions
Submitted by:
Sara Waddington
Taiwanese press specialist, Chin Fong, has placed smart machinery at the heart of its technological innovations. From a single-press smart solution, the company has moved on to multi-press connections and cloud computing, linking ERP management and even AI computing systems to analyse Big Data.
“Intelligent transformation is the key to a customer’s future success. During decades of experience in equipment manufacturing, we have encountered numerous customer cases involving automation integration of large production lines. We help clients to plan their robot/AGV/ARV/AOI automation applications according to their needs and different stages of transformation,” Chin Fong told ISMR.
It has done this through professional machine selection consulting services, combined with its “iForming PMS - Intelligent Forming Productivity Management System" solution. In response to ever-expanding customer requirements, the company has also implemented scanning code and fingerprint authentication to meet workplace safety requirements, as well as facial recognition and an iris recognition system.
“iForming is an intelligent forming solution which enables customers to quickly and cost-effectively introduce intelligent applications. Whether it is a generic stamping press, transfer press, forging press or servo press, all can be integrated into one platform, enabling Chin Fong presses to provide customers with a smart manufacturing solution for forming,” explained Chin Fong.
From a specification standpoint, this smart forming solution presents production process data in real-time through visual plant management software and a hardware interface (also known as a Real-Time Situation Room). These can be used as a reference for production processes, manufacturing management and decision optimisation to transform a traditional stamping factory into a smart production model.
“Smart transformation should never be a headache. It should be the solution. We are committed to helping our customers improve their manufacturing processes through smart manufacturing and Industry 4.0. Our smart management system updates supervisors on the progress of their factories in real-time. This improves traditional manpower and equipment management, which then extends to materials and logistics management, and finally leads to the factory smart 4M1E (Man, Machine, Material, Method and Environment) management method,” added the Taiwanese stamping specialist.
Accessible and convenient
This innovation was spurred by Chin Fong’s observation that most of its customers were concerned about the high cost of introducing smart management solutions in their initial stages of transformation and development, not to mention the time, cost and risk. It therefore developed its own iForming PMS system solution and implemented this in its own factory, serving as a technology demonstrator. As the goal is to make smart manufacturing more accessible for customers, iForming PMS solutions currently come with the machines as added value (not as additional products).
After-sales service is an important milestone in Chin Fong’s smart transformation solution. Its sales staff visit customers, and their engineers and service staff, to collect feedback and address technology-related customisation needs. In response to customers' remote maintenance needs, Chin Fong provides after-sales service via a mobile device app, so that data can be updated online. The press specialist has also worked with a third-party system provider to develop a common application-programming interface (API). This program combines enterprise and resource planning with a manufacturing execution system (ERP/MES) to respond quickly to changes in the production process. Management decision-makers can therefore integrate this into the shop floor tracking system (SFT), linking data in a more compatible and convenient way.
“iForming not only improves supply and demand forecasts, but also affects response time. It gathers historical information through Big Data and introduces AI machine learning. iForming integrates instant messages to notify customers proactively, which means an actively growing and intelligent system exclusively for customers. Recently, we collaborated with ASUS and Axiomtek to create an intelligent forming defect detection solution, which is the latest upgrade of iForming’s extension suite,” explained Chin Fong.
The "Intelligent Forming Defect Detection Solution" is based on iForming’s management system. It combines AI visual inspection system and AI edge computing for real-time production data and quality information aggregation, as part of iForming’s extended functions. The solution also features wave pattern detection capability.
“By absorbing a small amount of defect data through a special algorithm, the inspection system can automatically learn and calculate other defect possibilities so that defect detection accuracy can reach over 97%. By observing the waveform, it can also detect vibration and even noise abnormalities, and quickly report the inspection results through the firewall-equipped Ethernet and private cloud. It can also display this data on the Real-Time Situation Dashboard for 24-7 intelligent factory management,” concluded Chin Fong.
The Intelligent Forming Productivity Management System (iFPMS) solution for the stamping industry was recognized with a 29th Taiwan Excellence Award in 2020. Established in 1948, Chin Fong Machine Industrial Co., Ltd. is one of the top five press manufacturers in the world.
“To date, 100% of customers who have imported iForming have renewed their orders with additional features, which means that customers are really using this smart production model and finding it extremely useful. In the future, by standardising popular features, we will not only reduce the cost of implementation for customers, but also enhance the added value of the product and develop a customised solution for each customer,” Chin Fong told ISMR.
For further details, see www.chinfong.com