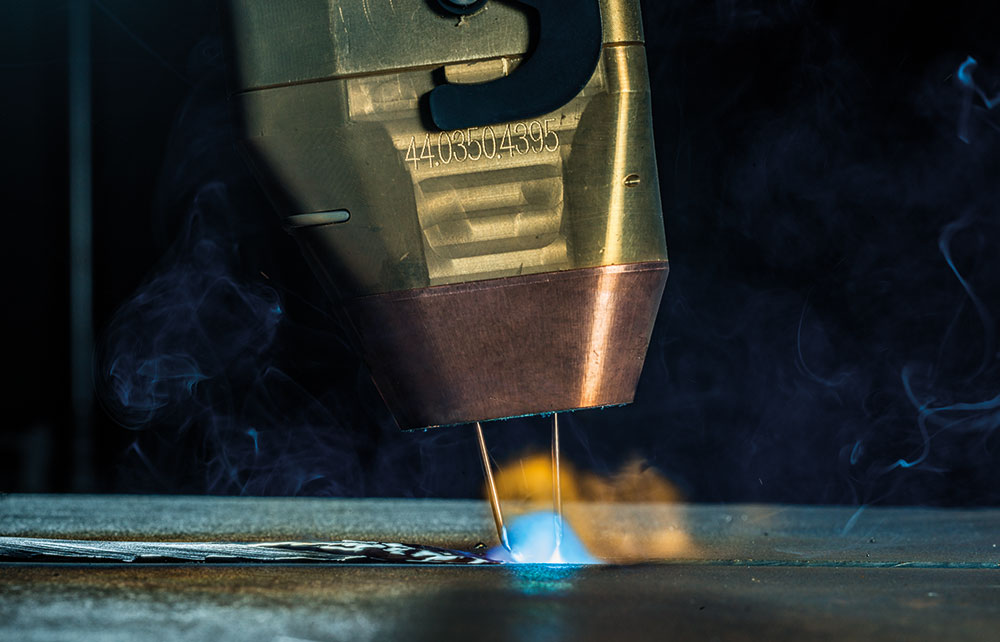
Fronius - TPS/i TWIN Push Tandem Welding
Submitted by:
Sara Waddington
When welding high-volume components or long seams, efficiency is the main challenge. High-performance welding makes this possible with its high deposition rates.
“Our TPS/i TWIN Push high-performance welding system is compact, easy to use and network-capable. Users profit from high deposition rates, high welding speeds and increased efficiency in production due to the reduced need for pre-fabrication and rework,” welding specialist, Fronius, told ISMR.
High-performance welding is characterised by a high deposition rate that enables strong weld seam volume or rapid welding speeds. This is particularly relevant when joining high-volume components or long seams for construction machinery, commercial vehicles, automotive parts and shipbuilding.
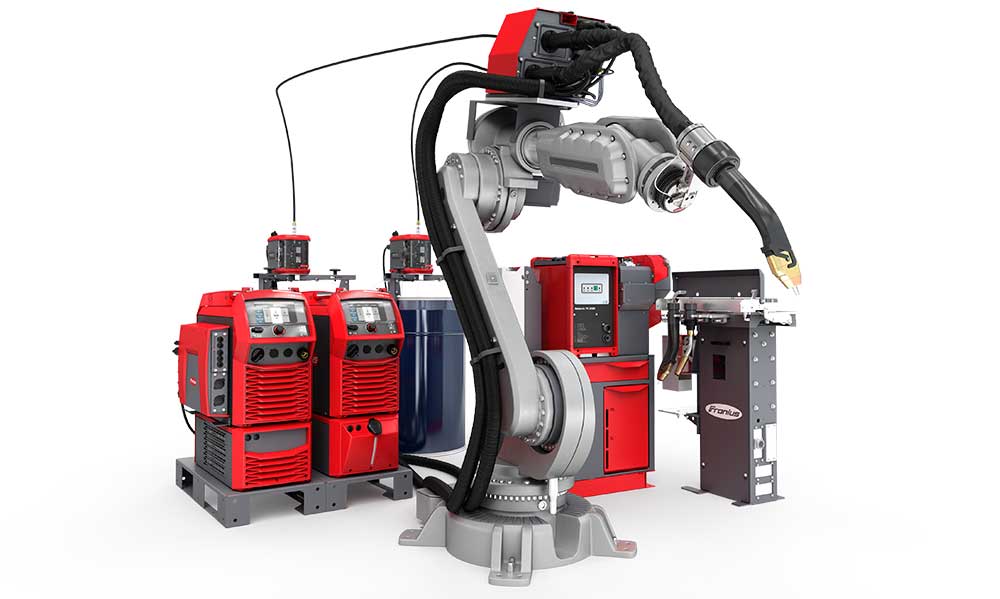
“The high processor power of the TPS/i improves the synchronised TWIN Push tandem process, making the process even more stable and reliable. Enhanced gap-bridging ability saves the user time at the component preparation stage. The amount of rework can also be reduced, since precise control of the welding process enables controlled droplet detachment and low heat input into the component, leading to low-spatter results with minimal distortion,” added the manufacturer.
Fronius offers new process and control options with the TPS/i TWIN Push: PMC (Pulse Multi Control) TWIN features a short, focused pulsed arc that is designed to enable improved penetration and a higher welding speed. The PulseSync option allows the user to select widely varying travel speeds for the two wire electrodes for greater flexibility to adjust welding parameters to the component and achieve higher welding speeds. The power source will automatically correct all relevant power source parameters, such as the ignition properties, the point of droplet detachment and the pulse ratio.
“New control mechanisms assist the welder in other ways too – the arc length stabiliser and the penetration stabiliser increase process stability and make it easier to configure parameters. Where the position of the interface varies, possibly due to component distortion or imprecise clamping, automatic seam tracking is offered. During welding, the welding system transmits a seam tracking signal to the robot so that it can make corrections as required,” continued Fronius.
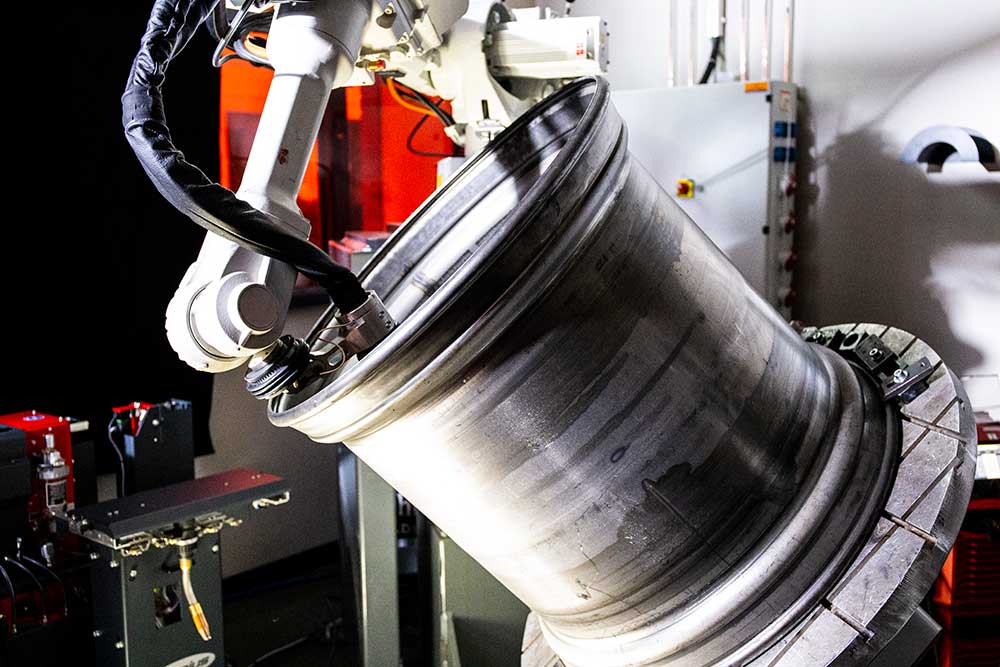
The TWIN process is based on tandem welding and features two wire electrodes that are fed into a welding torch with a single gas nozzle, but which remain electrically isolated from one another. As a result, the arcs can be controlled independently and, despite differing outputs, can be precisely synchronised and coordinated. In addition to two TPS/i power sources, the TWIN Push system requires a TWIN Controller. The controller synchronises the welding process and acts as an interface that is compatible with all robot makes. The compact wirefeeder, cooling system, hosepack and TWIN welding torch complete the welding system.
“The cooling system for the torch has been improved, extending the service life of wearing parts. Alongside this, we have developed the Robacta TSS/i TorchServiceStation. This welding torch cleaning system combines a number of cleaning methods, including high-pressure cleaning, brush cleaning and magnetic cleaning as well as cleaning by means of a cutter. The professional torch cleaning device lowers the overall system costs by extending the service life of wearing parts,” added Fronius.
The efficiency of the welding system can be further increased by using the TX TWIN welding torch change station. The console enables automatic switching between TWIN and Single torch bodies. This means that the same system can be used to weld areas that are particularly difficult to access with the more compact Single torch body. The robot automatically changes the torch body – allowing for unmanned shifts.
Further details can be found on the Fronius website.
Subscribe to International Sheet Metal Review to receive 10 magazines per year, packed with the very latest industry news and product reviews.