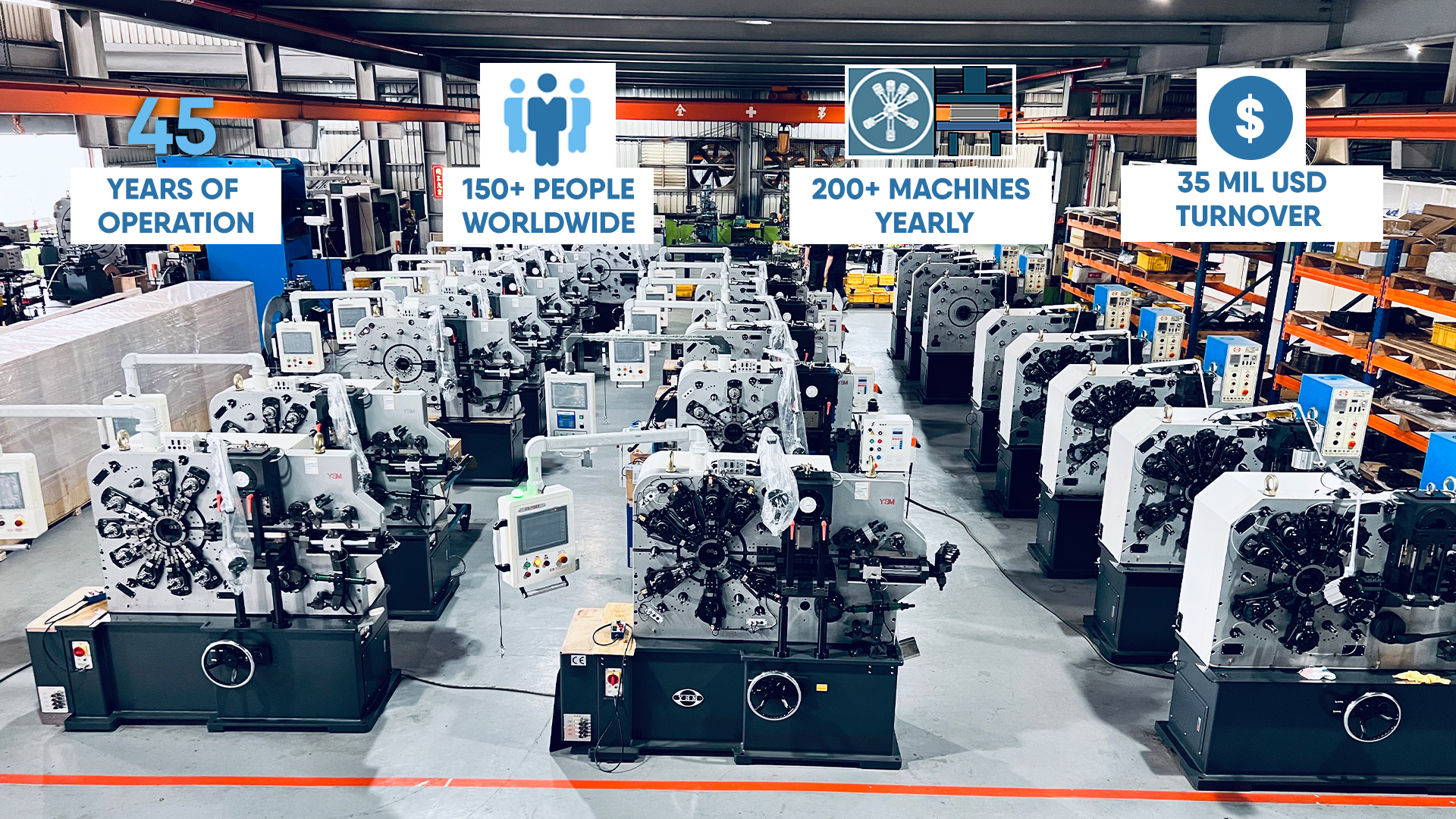
A modular philosophy
Submitted by:
Sara Waddington
In the September 2024 issue of ISMR, Gregory Wilfred, CEO of YSM International, highlights trends, drivers and challenges in global sheet metal markets and explains how they have influenced YSM’s culture of continuous innovation.
==
Taiwanese manufacturer, YSM, provides stamping and bending solutions. It is also a one-stop solutions provider in process automation; welding systems; thread-forming and inspection systems. With a workforce of over 150 people globally, it produces upwards of 200 machines to customers around the world.
YSM has placed a strong focus on tool design, continuous innovation and customer service in its global operations. Its headquarters are in Taichung (Taiwan) with various support facilities around the world, including a Technology Centre in India. YSM has delivered various projects in Asia and Europe, designed to remove its customers’ dependence on manual processes and operations by automating equipment.
Gregory Wilfred, CEO of YSM International in India, highlights trends, drivers and challenges in global sheet metal markets to ISMR and explains how they have influenced YSM’s culture of continuous innovation.
ISMR: Please give a brief background to YSM and highlight any notable successes and achievements over the past two-three years?
GW: Established in 1979, YSM today has evolved into one of the top three global leaders in providing stamping and bending manufacturing solutions. Our headquarters are at Taichung in Taiwan with other support facilities based in India, Indonesia, Turkey and other parts of the world.
We deliver cutting edge ‘high-tech’ and ‘low-investment’ manufacturing solutions. Our customers are our partners; our goal is to make lasting improvements to their manufacturing processes. We are here for the challenging tasks!
We support our customers by delivering stamping and bending solutions integrated with operations that need a secondary process such as thread forming; welding; sub-part assembly; riveting etc. All these solutions are delivered on a single production line capable of producing parts with speeds of up to 250 parts/minute.
Despite a difficult economic backdrop, we have recorded significant growth since 2022. Our turnover was almost 35 million euros last year, which we project will grow by 18%-20% this year.
ISMR: What are your views on the current global business climate for sheet metal professionals?
GW: The eurozone has bounced back from its shallow technical recession after a stronger than expected performance by its ‘big four’ economies in the first three months of 2024. However, I see more optimism in the North- American market (Mexico, Canada and USA). Investment, however, could be better.
The markets recovered well after COVID downturns in 2021 then, in 2022, the Russia-Ukraine war broke out and markets went down from May/June. We are now seeing recovery from these effects. For us, as a company, the key drivers in the sheet metal industry are below:
- Technological advances: Innovations and advances in stamping and bending technology. For example, we introduced our Radial and Linear line in one set-up to give the customer more manufacturing flexibility. There was a good response to these machines from the European market.
- Global economic conditions: Asia has been a particularly price-sensitive market. For example, we completed a project to cut production costs to give the benefit of cost savings to our Asian customers. Using tool standardisation, we were also able to optimise production tasks for tooling by turning out quicker designs and delivering faster and more economical tools.
By focusing on these two areas, we stay ahead of the game by listening to our customer needs and adjusting our business working operations accordingly.
ISMR: What is your strategic and technical focus for the company?
GW: We are always searching for the best way to manufacture a part. With this in mind, some of the key drivers for us have been in the areas below:
- Speed of production: Using new technology servo motors, we offer customers production speeds of up to 300 parts/minute. By employing multicavity technology for some parts, we are giving the customer the ability to produce up to 1200 parts/minute (300 x 4).
- Modular systems: YSM can provide solutions for all the secondary operations that need to be done after stamping and bending operations. We can integrate several complex secondary operations in line with the stamping and bending operations.
ISMR: What, in your view, are important industry trends and challenges? How are you responding to these?
To read the rest of this interview, see https://joom.ag/1myd/p70
ENDS