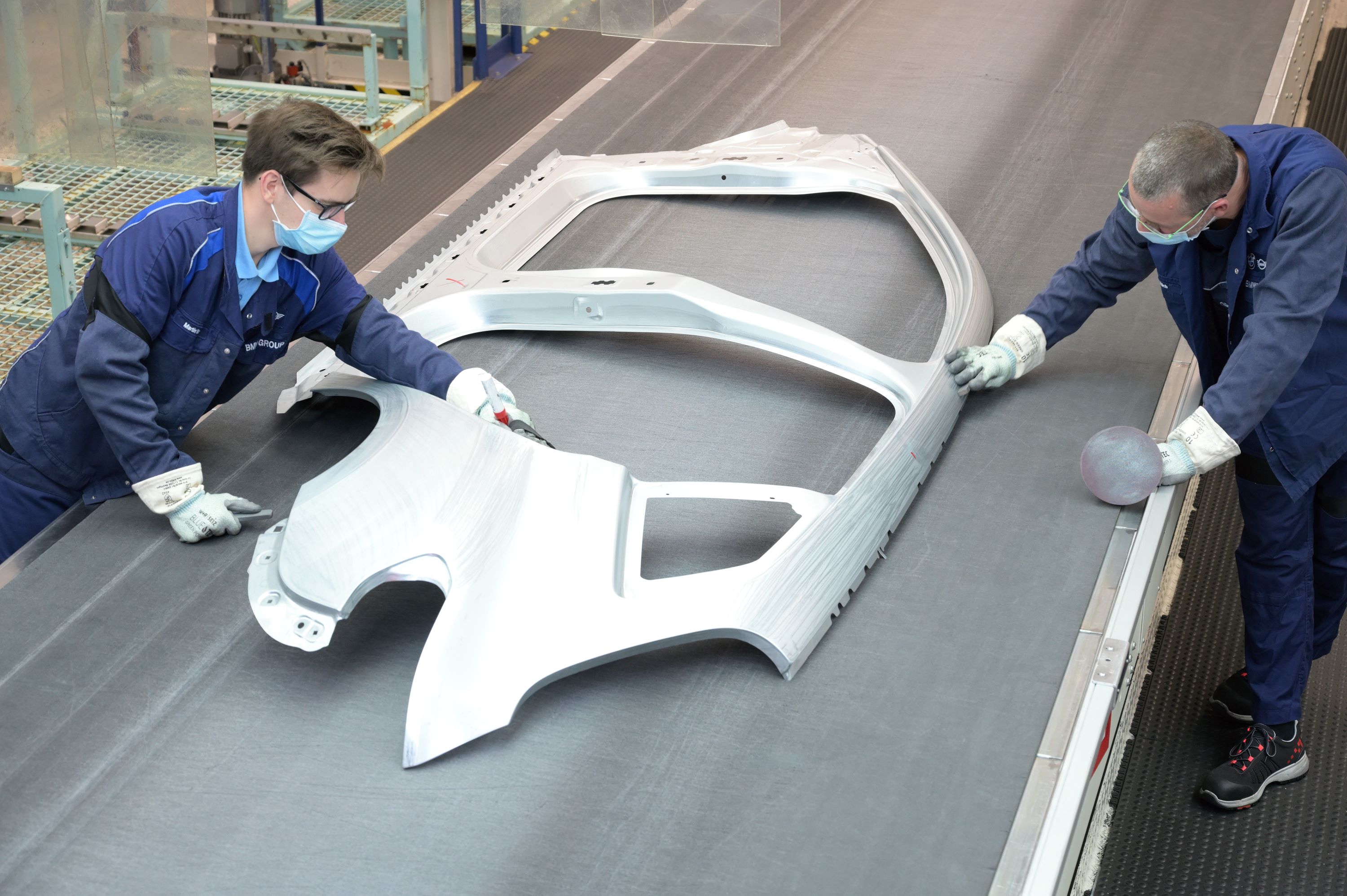
New BMW press shop at South Carolina plant
Submitted by:
Sara Waddington
BMW will invest more than US$ 200 million to construct a 219,000-square-foot press shop at its South Carolina plant in the U.S. The investment includes more than 200 new jobs. The announcement was made by BMW Manufacturing President and CEO, Dr. Robert Engelhorn, at the South Carolina Automotive Summit in Greenville, SC, USA.
The new press shop, which will start production in the summer of 2024, will take raw coils of steel, cut them into blanks and stamp sheet metal parts for future BMW models. Those components include hang-on parts such as the vehicle’s four doors, fenders, exterior body sides and lift gate.
A modern press shop requires manufacturing jobs with advanced-level training. These jobs include tool and die technicians, electrical and mechanical maintenance for automated machinery and specialised line operators. More than 45 Plant Spartanburg associates are currently training at BMW Group press shops in Leipzig, Germany and Swindon, England. These associates also train with partners from the Schuler Group which manufactures automated servo press lines for all BMW Group plants.
“Inside our global production network, we share best practices and train associates to the highest BMW standards. The cross-functional collaboration is part of our BMW culture,” said Karl Loessl, Vice President, Body Shop, BMW. “This world-class training will allow our associates to work with advanced technologies and systems and support our production of future models.”
The press shop marks the beginning of the automotive production process. Large steel coils arrive at the press shop, where they are unloaded from trucks using 55-ton overhead cranes. The steel coils are then fed into the blanking line, where the steel is cut into individual “blanks” (rectangular cut-offs or special shapes). These blanks are then ready to be fed into the press line.
Plant Spartanburg’s press line will consist of five press (stamping) stations. The line will be equipped with servo technology, which enables BMW to significantly increase the output performance of the presses. Using an overhead crane, each station is loaded with the correct press tool (die). The blank is fed into the first press station and transferred from one station to the next by a crossbar feeder robot for additional forming and trimming operations. The press line can run up to 18 strokes per minute. After the parts are stamped, they go to quality control for inspection and are then stacked into racks ready for delivery to the body shop production line.
“An onsite press shop is part of BMW’s localisation strategy to produce major parts at the location where we need them,” said Dr. Engelhorn. “This ensures the highest quality, efficiency and consistency in body shop parts for our customers.”
While Schuler will manufacture the automated press line, all tooling for Plant Spartanburg’s press shop will come from BMW tool shops in Eisenach, Munich and Dingolfing.
Since 1992, the BMW Group has invested nearly US$ 12 billion in its South Carolina operations. BMW Manufacturing is the largest BMW Group plant in the world, producing more than 1,500 vehicles each day and 433,810 vehicles in 2021. The plant exports nearly 60 per cent of its vehicles to about 120 global markets.
The model portfolio includes five BMW X models, four Motorsport X models and two plug-in hybrid electric vehicle X models. The BMW XM, the first electrified high-performance hybrid model in the BMW M portfolio, will begin production in late 2022. The factory has an annual production capacity of up to 450,000 vehicles and employs more than 11,000 people.