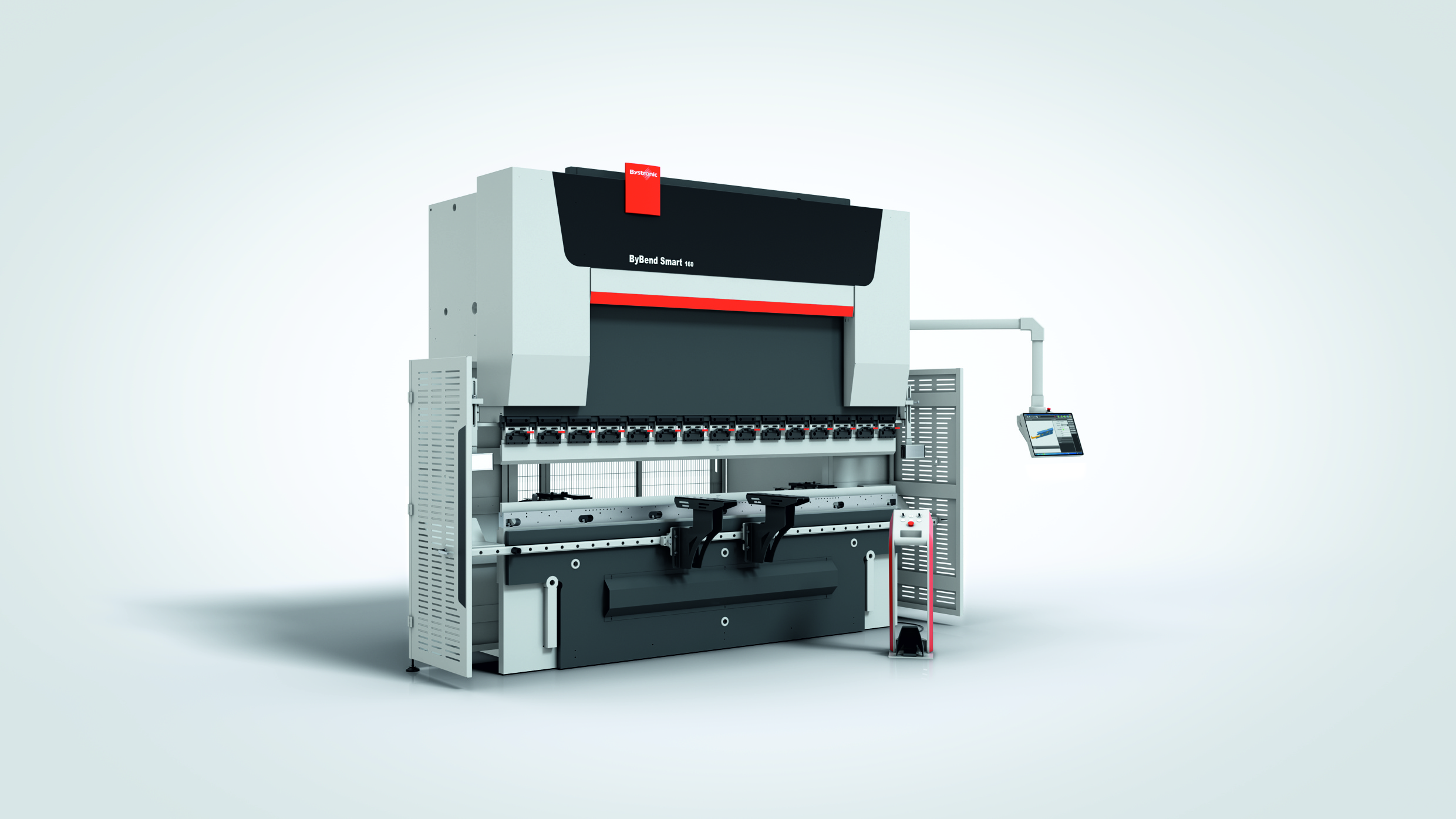
New ByBend Smart
Submitted by:
Sara Waddington
The new ByBend Smart from Bystronic increases the flexibility and, in particular, the speed of bending.
“The ByBend Smart offers high-quality Swiss bending technology and numerous new functions at an affordable price. This is its recipe for success,” said the Swiss manufacturer. “The new press brake offers numerous additional functions and is now even more versatile for an even wider range of applications. It is 30% faster than conventional bending, and even 50% faster with the new ‘Efficiency Booster’ option. This makes it suitable for all those sheet metal processing companies for whom time is a crucial factor in the day-to-day competition for orders,” it added.
One of the ByBend Smart’s flexibility-enhancing features is the insert and stroke length expansion. This upgrade, which is available with the purchase of a new machine and extends the insert height for bending tools from 480- to 580mm. The additional 100mm boost the ByBend Smart’s flexibility by as much as 30 per cent because this means that higher tools can be used, which enables users to produce parts with lower bending edges. This is particularly useful when bending boxes and drawers.
“Another new optional feature is the five-axis back-gauge. Until now, users had the choice between a two-axis and a four-axis back-gauge system. Users who choose the five-axis system can now also use the ByBend Smart to bend complex 3D parts. For example, sheet metal products where the bending edges are not just parallel, but also at angles to each other. Similar to the expansion of the insert height and stroke length, the various back gauge systems represent an option to increase the bending versatility. The basic version of the ByBend Smart comes with a two-axis back gauge system,” confirmed Bystronic.
In addition to a wide spectrum of applications, fast bending sequences and short manufacturing cycles frequently play an important role for users. Here, increasing process speeds and shortening setup times are key. The new ‘Efficiency Booster’ is an optional feature that ensures rapid return of the upper beam, speeding up the bending process by up to 20%.
The machine’s main drive is only active when the machine is actually in operation. This is the logic driving the ‘Energy Saver’ which reduces the power consumption of the machine while also boosting productivity and minimizing noise/waste heat.
On request, higher-performance mechanics are available that enable the ByBend Smart’s upper beam to move at higher speeds during the rapid movement and bending phases. The “Fast Bend M Safety System” option consists of a laser safety system that allows the upper beam to move almost all the way to the part that is being processed at the rapid movement speed. The high-precision laser sensor allows the ByBend Smart’s control to reduce the upper beam’s speed from up to 200mm per second (rapid movement speed) to 16mm per second (bending speed) just before reaching the metal sheet. The laser safety system functions like an intelligent brake assistant that permits the machine to move at a higher speed for longer. This offers users a speed advantage of up to 30 per cent, said Bystronic.
Dynamic sheet support is designed for machines with a press force between 100 and 300 metric tons. The lifting capacity is 100kg per set (at a distance of approx. 800mm from the bending line). The dynamic sheet follower is operated simultaneously with the upper beam. It increases material handling flexibility, in particular for small batch sizes with changing material types and thicknesses.
Optionally, there are rollers available for heavy parts. The table can be converted from plastic rails to rollers or brushes in seconds. The optional functions are available in three special packages, which are tailored to the needs of the individual users: Comfort, Productive and Tropical packages.
The ByVision Bending user interface is included in the ByBend Smart’s basic version. Operators launch all the bending processes with a few swipes of the finger on a 22-inch touch screen. ByVision Bending has an extensive database that includes the parameters for all the common types of sheet metal and bending tools. Depending on the material thickness and bending angle, the user interface determines the ideal bending process and suggests the suitable tools.
“Dynamic crowning ensures high-precision air bending results. This unique assistant function is only available in this form with press brakes from Bystronic. The ByBend Smart’s crowning recognizes the position and length of the sheet metal part. This sensor system is integrated directly into the ByVision Bending control, enabling the ByBend Smart to automatically ensure the ideal distribution of the bending force across the entire bending length without requiring the operator to deal with complicated details. This results in precise and consistent angles with every bend,” concluded Bystronic.
Link to Youtube video : https://www.youtube.com/watch?v=n_PmcVBs27Q
Find out more on: bybendsmart.bystronic.com (see https://www.bystronic.com/en/products/pressbrakes/ByBend-Smart.php )