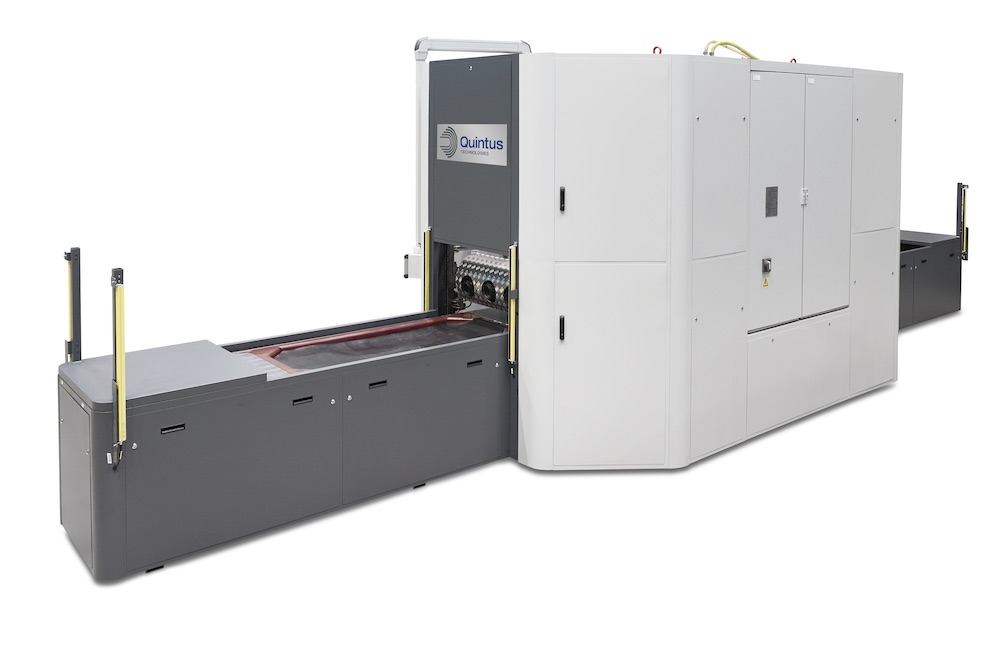
New trainer aircraft drives investment in flexible forming technology
Submitted by:
Sara Waddington
Header image: An 800-bar (11,600 psi) Flexform press from Quintus Technologies entered service at Piper Aircraft’s Vero Beach, Fla., manufacturing facility in the fourth quarter of 2019.
Piper Aircraft Inc. has installed a high pressure Flexform™ press from Quintus Technologies at its manufacturing facility in Vero Beach, Fla (USA). The addition of the press reflects the growing market for new trainer aircraft, spurred by the current pilot shortage and the upsurge in training needs according to the aircraft manufacturer
“Piper is the only aircraft manufacturer to offer a complete line-up of training aircraft and, with a global pilot shortage, we have seen a resulting increase in demand for our training products. It is paramount that we have modern, reliable and cost-efficient equipment to help us meet the increase in our production,” stated James Funk, Piper’s Chief Operating Officer. “With its capacity and ease of use, the new Quintus press is helping us to manage our growth while controlling costs and improving quality.”
The Quintus QFC 0.7x1.8-800 fluid cell press applies flexible forming technology to the production of sheet metal parts across the entire Piper line of eight aircraft models. It supports thousands of part numbers, many with complex geometries or free-form surfaces. The high forming pressure--800 bar (11,600 psi)—ensures close-tolerance parts direct from the press, with little or no secondary hand-work required.
With a work area of 27.6 x 73 inches (700mm x 1800mm), the press introduces several production efficiencies by eliminating forming operations, intermediate heat treatments and manual pre- and post-forming operations.
“The Flexform process utilises a combination of a single rigid tool half, which operates in conjunction with a flexible rubber diaphragm under uniform high hydrostatic pressure, to form sheet metal parts with accuracy and repeatability. This design approach generates significant tool cost savings and speeds up tool production, especially for intricately shaped components,” Quintus Technologies told ISMR.
“We believe that the ability to combine a higher level of forming die design with modern high- pressure forming technologies will provide substantial time and cost savings as Piper ramps up its production,” noted Ed Williams, General Manager – Americas, Quintus Technologies.
Piper supplemented its press order with a long-term Quintus® Care Programme for application support, high availability of spare and wear parts, along with guaranteed and prioritised technical support. It also includes both annual press inspections to maintain its status and annual training and recertification of Piper personnel to maintain and elevate their skills.
Quintus Technologies designs, manufactures, installs and supports high-pressure systems for sheet metal forming and densification of advanced materials. The company is headquartered in Västerås, Sweden, with a presence in 45 countries worldwide.
The Trainer Class Pilot 100/100i, Archer TX, Archer DX, Arrow, Seminole and Seneca V aircraft form the most complete technically-advanced line of pilot training aircraft in the world. Piper is a member of the General Aviation Manufacturers Association.