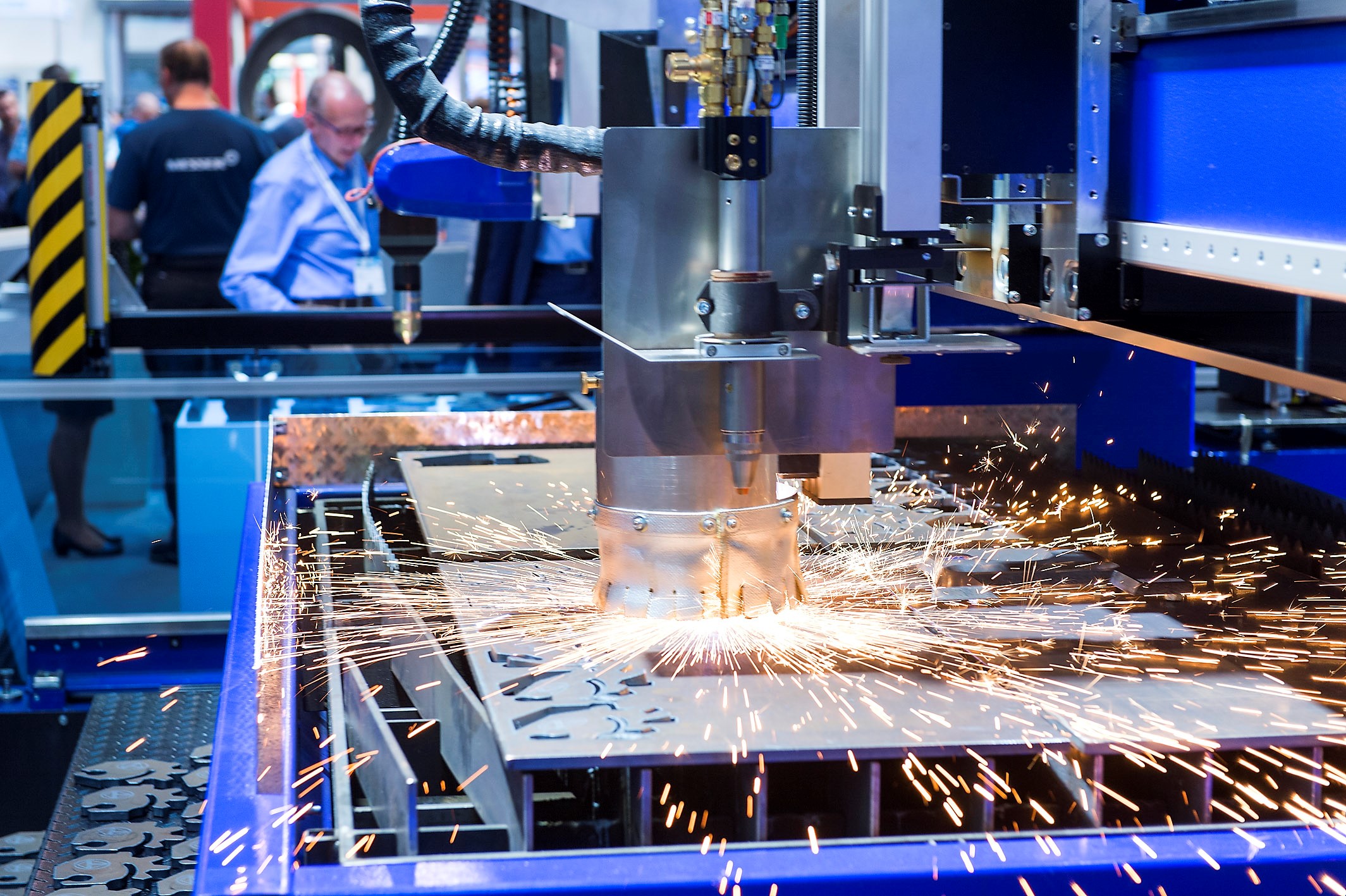
The plasma process
Submitted by:
Sara Waddington
In the December 2023, January 2024 issue of ISMR, we outline the principles and benefits of plasma cutting as well as key features and process variations.
=========
Electrically conductive, ionized gas is called plasma. The plasma cutting process, used in the cutting of electrically conductive metals, utilises this electrically conductive gas to transfer energy from an electrical power source through a plasma cutting torch to the material being cut.
The plasma arc formation begins when a gas such as oxygen, nitrogen, argon or even shop air is forced through a small nozzle orifice inside the torch. An electric arc generated from the external power supply is then introduced to this high-pressured gas flow, resulting in what is commonly referred to as a “plasma jet”. The plasma jet immediately reaches temperatures up to 40,000° F, quickly piercing through the workpiece and blowing away the molten material.
Plasma cutting has long proved to be a flexible and cost-effective method of processing parts. The plasma process can cut aluminium, mild steel, stainless steel and tough wear-resistant materials from as little as 1mm thick through to 60mm. Plasma cutting can really shine in some niche applications, such as cutting expanded metal. Unlike the oxyfuel process, the plasma process can be applied to cutting metals which form refractory oxides such as stainless steel, aluminium, cast iron and non-ferrous alloys.
Plasma system components
A basic plasma cutter or plasma cutting system includes the following components:
Power supply: A constant current DC power source. The open circuit voltage is typically in the range of 240 to 400 VDC. The output current (amperage) and overall kilowatt rating of the power supply determines the speed and cut thickness capability of the plasma cutter. The main function of the power supply is to provide the correct energy to maintain the plasma arc after ionization.
Pilot arc starting circuit: In most liquid-cooled torches of 130 amps and higher, this is a high- frequency generator circuit that produces an AC voltage of 5,000 to 10,000 volts at approximately 2MHz. This voltage creates a high-intensity pilot arc inside the torch to ionize the gas, producing the plasma. Rather than the high frequency starting circuit, air plasma torches typically use a moving electrode or “blowback start” technology to ionize the gas.
Torch: This serves as the holder for the consumable nozzle and electrode. It provides cooling (either gas or water) to these parts. The nozzle and electrode constrict and maintain the plasma arc.
Other elements can include a cutting bench, exhaust system and coolant circulation system.
Plasma cutting in focus
Plasma cutting applications include straight cutting; bevel cutting; gouging; hole cutting; extended reach cutting; fine feature cutting and marking.
Precision plasma systems (high current density) are designed and engineered to produce the sharpest, highest quality cuts achievable with plasma. The torch and consumable designs are more complex, and additional pieces are included to further constrict and shape the arc. Multiple gases, such as oxygen, high purity air, nitrogen and a hydrogen/argon/nitrogen mixture, are used as the plasma gas for strong results on a multitude of conductive materials.
The basic plasma arc cutting system consists of a power supply, an arc starting circuit and a torch. These system components provide the electrical energy, ionization capability and process control that is necessary to produce high-quality, highly productive cuts on a variety of different materials. The power supply is a constant current DC power source. The output current (amperage) of the power supply determines the speed and cut thickness capability of the system. The main function of the power supply is to provide the correct energy to maintain the plasma arc after ionization.
The arc starting circuit is a high-frequency generator circuit that produces an AC voltage used to create a high-intensity arc inside the torch to ionize the gas, thereby producing the plasma. The torch serves as the holder for the consumable nozzle and electrode, providing cooling (either gas or water) to these parts. The nozzle and electrode constrict and maintain the plasma jet.
Modern machine designs
“Early CNC profiling machines were fitted with single or multiple oxyfuel cutting heads. These were built using large heavy castings and/or structural beams and driven around at relatively slow speeds using gearboxes with large motors – and such machine designs are still available today. Modern high-speed precision plasma cutting machines need to be able to accelerate, decelerate and change direction in a smooth, controlled and vibration-free manner. This requires a more refined machine design that includes a variety of features,” commented Kerf Developments.
Some of the key components to form modern plasma machine designs include:
To read the rest of this article in the December 2023/January 2024 issue of ISMR, please see https://joom.ag/yond/p32