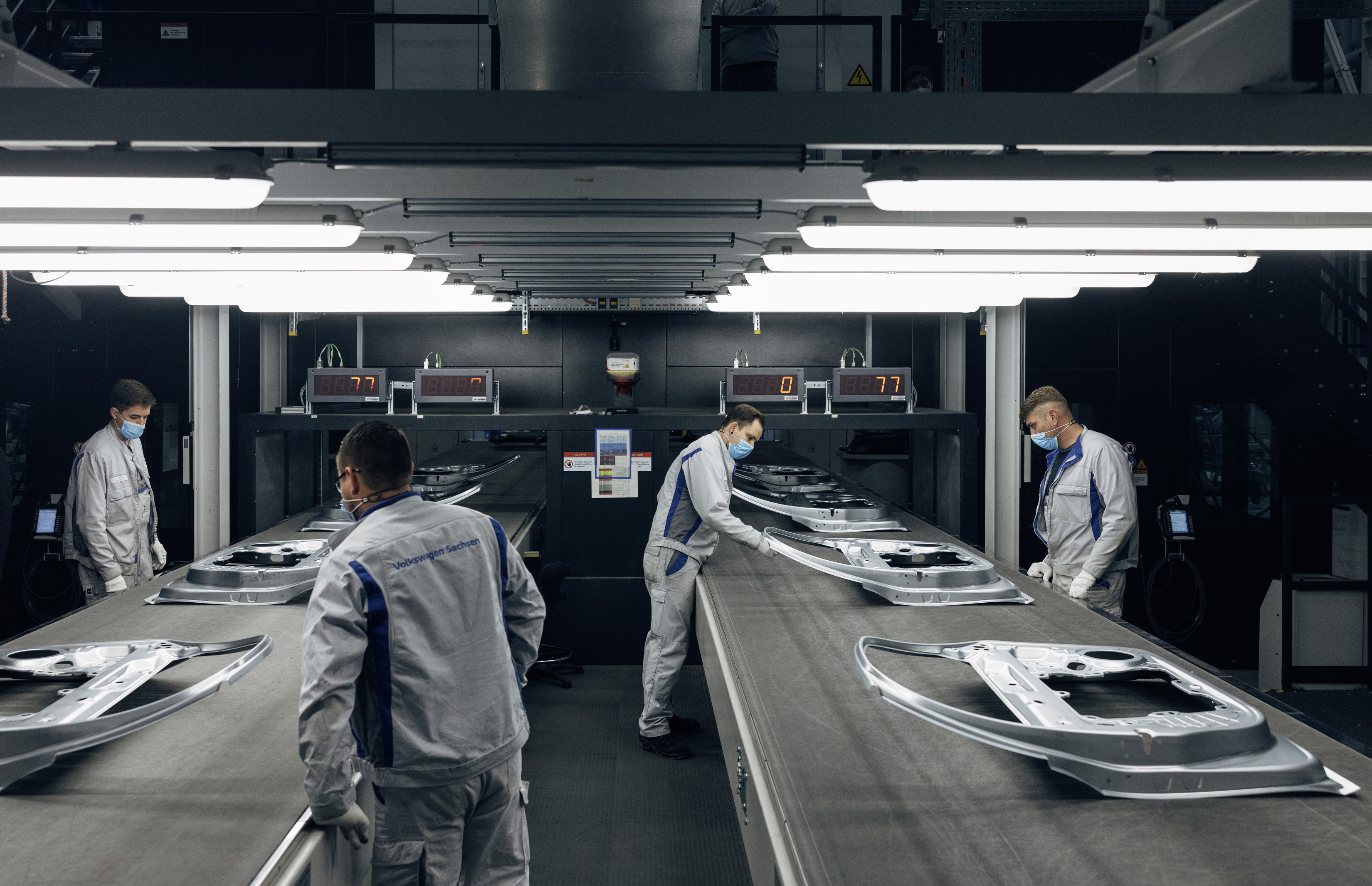
Press shop expansion for Volkswagen
Submitted by:
Sara Waddington
Caption: The first new outer skin parts for the ID. Vehicles from the new large press at the Zwickau vehicle plant.
Volkswagen has now officially inaugurated the press shop expansion in its electric car plant in Zwickau, Germany. As of now, the complete outer skin for the six electric models produced in Zwickau will be pressed on-site. The €74 million investment will enable further gains to be made in reducing the carbon footprint of the ID.31 and ID.42 vehicles.
“The effect is remarkable: more than 9,000 fewer direct truck journeys each year from now on for body manufacturing and annual savings of 5,800 tonnes of CO2. This will create 60 new jobs in the factory,” explained Volkwagen.
The official opening recently was attended by Minister President of Saxony, Michael Kretschmer, in the company of Christian Vollmer (member of the Board of Management with responsibility for production and logistics for the Volkswagen brand); Dr. Stefan Loth (Chairman of the Board of Management of Volkswagen Saxony) and Jens Rothe (Chairman of Volkswagen Saxony’s Central Works Council).
“The goal is to achieve carbon-neutral production at all MEB locations in Europe, as is already the case at the Zwickau plant. Zwickau is the pioneer and role model in this respect. The new press shop is an important milestone on our ‘Way To Zero’ journey, through which we are aiming to reduce the environmental impact of our production by 2025 - in areas such as energy usage, CO2 emissions, waste and the use of water – by 45% per vehicle compared with the baseline year 2010. 90% of all Volkswagen Passenger Cars locations purchase electricity from renewable sources. With our ‘Zero Impact Factory’ environmental programme, production-related emissions are being reduced consistently at all factories, as well as in logistics,” commented Christian Vollmer during the ceremony.
The €74 million invested in expanding the press shop represents one of the largest single investments in the course of transforming the site. In addition to a press in XL format, an automatic stacking line and a 30m high bay warehouse for logistics have been put into operation on the extra 8,400 square metres of space. The high bay warehouse alone cost €23 million.
From now on, all required outer skin body parts, such as doors and boot lids, can be pressed on-site for the electric models produced in Zwickau. Delivery from other locations, such as Emden and Wolfsburg, will cease. More than 9,000 truck journeys will be avoided each year and CO2 emissions reduced by 5,800 tonnes – this corresponds to a share of 16% of the direct truck volume for body manufacturing at the Zwickau plant.
The new XL press from Schuler weighs more than 1,000 tonnes, with a press force of 6,900 tonnes across five stages. With 10,800 press strokes a day, the 92-metre long, 22-metre wide and 12-metre high press is designed for high speed and efficiency. It is the first time that a press with a mix of conventional and servo technology has been used in the Volkswagen Group. After its parent plant in Wolfsburg, the Zwickau facility now has the second-largest press shop within the Volkswagen brand. Around 20 million parts per year have been produced on average in West Saxony in the past ten years. With the new XL press, this figure is set to increase to up to 30 million parts per year by the beginning of 2022, some of which will continue to be supplied to other Group sites. Transformation of the site will be completed in 2021.
Zwickau is playing a key role in the system change towards electric mobility: for the first time, said Volkswagen, a large car factory is being completely re-equipped for electric mobility with an investment of some €1.2 billion. All conversions will be completed on schedule this year. In addition, both production lines in assembly were converted. Zwickau has around 1,700 robots in body manufacturing and assembly, driverless transport systems and fully automated production processes.
The ‘Way To Zero’ is the brand’s master plan for emission-free mobility for everyone. The journey began in 2020 with the market entry of the ID.3. Meanwhile, the global rollout of the world car on the MEB platform will focus this year on the ID.4. Over the coming years, Volkswagen will offer emission-free mobility in all segments with the ID. family. The brand plans to build at least 1.5 million e-cars annually by 2025 and reduce their carbon footprint by 30%. The goal is to be fully carbon- neutral by 2050 – in terms of both products and the company.