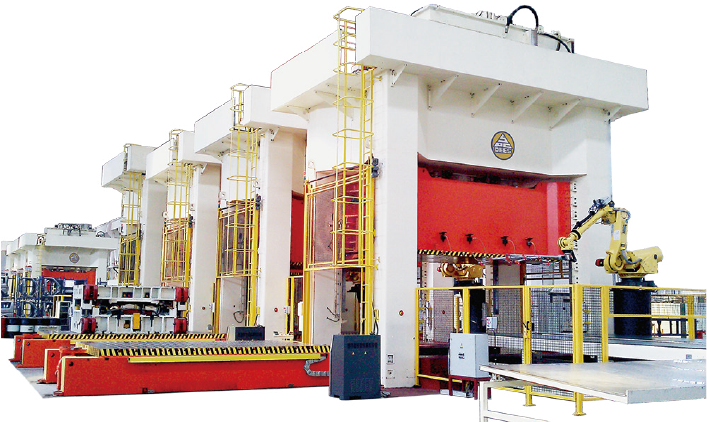
Pressing for action
Submitted by:
Jordan
We highlight an alphabetical selection of the latest new global stamping, tooling and pressing innovations.
===
The global metal stamping market was valued at US$ 215.28 billion in 2024 and is projected to reach US$ 324.70 billion by 2034, expanding at a CAGR of 4.20% from 2025 to 2034 according to analyst Precedence Market Research. By region, Asia-Pacific dominated the global market in 2024 with a 36% market share. By product, the blanking segment held the largest market share in 2024.
Metal stamping, or pressing, converts flat metal sheet (or blanks), as well as coil, into specific shapes. It is a complex process that includes several metal forming techniques such as blanking; punching; flanging; drawing; embossing; trimming; coining and piercing. Stamping dies are the tools that shape and cut sheet metal parts.
“Innovations in metal stamping processes have brought about improved efficiency and accuracy, with techniques such as progressive and transfer stamping leading the way for market expansion. One significant trend propelling the metal stamping market is the integration of automation and robotics within manufacturing processes, boosting speed, precision and efficiency. Additionally, the renewable energy sector's expansion spells a higher number of opportunities for the market as there is a surging requirement for metal components in renewable energy infrastructure. The push for lightweight materials in the consumer electronics space is also contributing to increased demand for metal stamping services,” outlined market analyst, Research and Markets.
Some of the most common types of metal stamping machines include mechanical, hydraulic, hydroforming and servo presses that are fitted with multiple dies to cut and shape metal sheets of stainless steel and metals such as aluminium, zinc and copper. Better control, greater speed and versatility, shorter cycle times and higher energy savings are just some of the hallmarks of the latest technologies. In this article, we highlight an alphabetical selection of the latest new global stamping and pressing innovations.
Selected innovations
Italian stamping specialist, AIDA, promoted its range of press technologies at EuroBLECH in Hanover, Germany, last October. This included its DSF-NE2 monoblock servo presses as well as the entire AIDA press line series with servo presses, high-speed automatic presses for lamination and precision forming presses.
The AIDA DSF-NE2 is a monolithic two-point servo press that combines the high rigidity of the monoblock frame with the flexibility of the freely programmable servo movement of AIDA DSF® technology, Direct Servo Former®. AIDA’s AET (AIDA Electronic Transfer) solution enables the movement of blanks and parts in multi-station or interconnected presses. It was designed for retrofit installations and can be integrated to all brands of mechanical and servo presses. AIDA’s DSF-TE4 servo transfer presses (double-column split presses designed for transfer applications) offer high levels of customisation through multiple configurations.
Two product lines that are dedicated to the production of motor laminations are the AIDA HMX Series and AIDA MSP Series presses. The AIDA MSP lamination press is designed for production of precision and high value-added motors such as EV motors, HEV motors and energy-efficient home appliance motors. The MSP-4000-430 high-speed press was launched in early 2024, specifically for die lengths of up to 4,300mm as required for triple-row production.
At EuroBLECH 2024, Swedish press specialist AP&T introduced its latest innovation, AP&T® SkyLines – a compact and efficient press-hardening line, specially developed to handle large and complex components.
“The industry is increasingly moving towards sustainability and energy efficiency, and the new AP&T® SkyLines combines precision with short cycle times, making it attractive to customers looking to improve both efficiency and quality in their production. With our broad range of services, SkyLines also provides high performance over time, which creates long-term business value for our customers,” AP&T told ISMR.
AP&T celebrated sixty years in operation in 2024. Its global offering includes complete production lines with presses, linear automation, tools, heat treatment systems and services such as maintenance, spare part provision, optimisation and rebuilds.
It has introduced a new version of its servo-hydraulic press with even lower energy consumption than before. The new version is primarily intended for progressive die stamping which requires large numbers of strokes per minute and for other types of forming requiring precision such as embossing, punching and deep drawing. It has also introduced a new Android-based tool that simplifies remote problem solving and reduces the risk of misunderstandings and downtime.
Italian manufacturer Balconi Presseccentriche S.p.A. produces transfer, blanking and servo presses as well as presses for progressive tools, impact extrusion presses and fin die presses. Its press model 4DMRF-LD-2000 has a 2,000kN cushion and three-axis electronic transfer. The press can produce up to 27 strokes per minute.
Boldrini (part of the FACCIN Group) is a manufacturer of hydraulic dished-end presses, flanging machines and manipulators. The presses feature high speeds including approach, return and, particularly, pressure build-up timing that, it told ISMR, results in a substantial increase in head production.
Its heavy duty four-column dual use hydraulic deep drawing press has a capacity up to 5000 tons. The ROTEX design combines a hot forming press with a hot flanging machine capable of forming heads of up to 200mm in thickness.
Its manufacturing line includes specially designed hydraulic presses with one or more independent cylinders used for folding, straightening and shaping of components for naval, aircraft and aerospace applications. Hydroforming and/or air forming presses, used for multiple purposes, are also available.
Swiss stamping specialist, Bruderer AG, employs some 500 people all over the world, 390 of whom work at its Frasnacht site in Switzerland, where all its high-performance stamping presses are produced. Around 95% of the company’s products are manufactured for the export market. Its stamping presses include the BSTA 710-220 and BSTL 350-88 models (the latter for customers involved in volume production of small and miniature components)
“As a fixed-stroke press, the BSTL uses up to 30% less energy when compared to older machine models. It comes with a new-generation servo feed unit,” commented Bruderer. The BSTA 710-220, said Bruderer, offers “the longest bed length (2.2 metres) of its machine type in the world.” With automatic stroke adjustment and various options such as different stroke lengths, shut heights and press force monitoring (for example), the press can be configured for individual customer requirements.
Bruderer UK ran its BSTL 350-88 live at MACH 2024 in Birmingham, UK. It set up a full production line showcasing the machine’s capability in the volume production of small and miniature components.
Taiwanese manufacturer Chin Fong’s stamping presses range from 20-ton single crank presses and up to 3200 metric tons of capacity to four-point eccentric gear-driven, large panel and multi-stage transfer presses. Forging presses are further diversified by cold, warm and hot forging processes. It has also developed an intelligent single-crank press with a crank mechanism used for blanking, drawing, bending and partial forming. Its straightside double-crank power press, with 400-ton capacity, has a bed area of 2.5m x 1m and can produce metal stampings from material measuring up to 400mm wide and 3.5mm thick.
Established in 1948, Chin Fong now has offices in Taiwan, China, Indonesia, Malaysia, Thailand and the USA as well as representatives in numerous countries around the world. Its A0 tandem press line for the automotive industry includes stages such as deep drawing, trimming, piercing etc.
The company has moved onto multi-press connections and cloud computing, linking ERP management and even AI computing systems to analyse Big Data. It offers machine selection consulting services, combined with its “iForming PMS - Intelligent Forming Productivity Management System” solution. It has also implemented scanning code and fingerprint authentication to meet workplace safety requirements, as well as facial recognition and an iris recognition system.
Chin Fong has further boosted its sustainability credentials with the award of certification from SGS for ISO 14064-1 greenhouse gas and ISO 14067 Carbon Footprint for its C-frame press products.
COSKUNÖZ KALIP MAKINA SANAYI VE TICARET A.S. offers turnkey solution to OEMs for stamping tooling, with upstream and downstream services which include engineering feasibility at vehicle design stage; HLTO services; die repair and maintenance; prototype dies/parts and project management.
DEES Hydraulic Industrial Co., Ltd. is a hydraulic press manufacturer with factories in Taiwan and China. Its main products include presses such as custom triple-action; die spotting; die tryout; deep- drawing; transfer; servo controlled; tandem press line; hot forming four-post; hemming; C-frame hydraulic presses etc. Its focus is on three main stamping areas: servo motors, higher speed of the hydraulic press and higher productivity for presses, using accumulators for shorter strokes. DEES Hydraulic has also successfully developed a closed loop, hydraulic, servo-controlled die spotting press.
DEES has introduced a 24-hour 2,500-ton tandem line customised for automotive manufacturing industry. The hydraulic monoblock system is powered by a motor and pump set. The moving bolsters are enhanced with a QDS system (quick die-change system) to make the heavy die change easier and faster. Users can adjust pressure, speed, daylight and stroke distance.
The high-speed technology of the HD series developed by DEES is controlled by the accumulator. Its pressing speed is between 30-150mm/second, with an approaching speed of 800mm/second or faster and return speed of 600mm/second or faster. With the cushion system function to knock out the parts, all speeds and strokes including the slide and cushion systems are adjustable. DEES’s self-developed HD-FASTech technology has been designed to improve deep drawing/production efficiency.
DIEFFENBACHER showcased hydraulic forming presses and complete press lines for sheet metal forming and the production of high-quality stainless-steel parts at EuroBLECH 2024 in Hanover Germany. Digitalisation and sustainability solutions, along with service and automation expertise, were also highlighted.
Examples of applications produced with Dieffenbacher equipment include battery housings, battery boxes and underbody covers for many e-mobility applications such as drones and electric cars, and bicycle components such as frames and rims. AT JEC2024, it showcased processes including Sheet Moulding Compound (SMC) and GMT and its Tailored Blank Line, including tape-laying and consolidation technologies. The company’s core competence, the hydraulic press, plays a major role in all these processes. Its press lines feature press forces of up to 32,000kN.
The manufacturer’s digitalisation platform, EVORIS, uses artificial intelligence to make production lines faster and more efficient. The company celebrated its 150th anniversary in 2023.
ebu Umformtechnik (ebu) designs automatic punching machines, presses and automation from the conveyor system to parts management. Its HMI (human-machine interface) features a Siemens Unified Panel. The HMI is cloud- and web-ready and multi-touch gestures as well as zooming functionality is possible.
Fagor Arrasate, headquartered in Spain, offers presses, coil cutting and processing lines, and complete systems for manufacturing complex metal parts. It also specialises in composite forming, hot and cold forging systems, and press hardening. It is part of the Mondragon Corporation. It acquired a 70% stake in Spanish company, Ribinerf, which specialises in industrial robotics, 3D vision and artificial intelligence to automate part quality control, sorting, picking and racking processes.
Fagor Arrasate designs and manufactures presses and stamping systems from 630KN up to 150,000KN using mechanical, hydraulic or servo-driven technology. It has been supplying transfer presses for more than 30 years as well as manufacturing large transfer presses of more than 3,500 tons.
Its presses are fully automated, with its own automated systems such as transfer systems or pick-up destackers. It also offers one single control architecture for an entire press line. Its high-speed press line (WaveLine concept) has been developed to transfer large, stamped parts (such as body side, hood, roof and double-door units) through large tandem press lines. Fagor Arrasate has also incorporated Danobat’s coil laser-cutting technology into its press lines. It offers a modular and scalable coil-fed laser blanking concept.
FF Fluid Forming GmbH produces the FormBalancer hydroforming press. It shapes metal sheets into a tool mould by applying very high pressures (up to 4000 bars). The clamping forces of up to 8,000 tons required in this process are completely absorbed by the machine frame without any deformation of the tools, it told ISMR.
Turkish manufacturer, Hidrokar Pres Metal Makina İml. San. İç ve Dış Tic, manufactures a range of presses in different formats and dimensions, including hydraulic and deep drawing presses.
Fresan Makina san. ve Tic. Ltd. Sti manufactures C-frame eccentric presses from 10 tons to 250 tons (100kN - 2500kN), special machinery and hydraulic punching presses.
Group Rhodes, one of Europe’s largest OEMs in its field, showcased its latest innovations for hot and cold forming of metals and composites in the aerospace industry at the Advanced Engineering exhibition (30-31 October 2024) at the NEC, Birmingham (UK). As well as celebrating its 200th anniversary, the Group unveiled its latest advancements in superplastic forming and diffusion bonding, while highlighting its turnkey solutions for specialised machinery in the aerospace sector.
The Group significantly expanded its workforce in 2024 to meet the needs of its customer base across its four divisions. Most of these new appointments are in the company’s manufacturing and machining operations.
The Group actively manufactures and markets over fifty basic ranges of presses/machines and designs, develops and manufactures bespoke machinery and complete turnkey solutions. Press examples include flexible die presses and stretch forming presses. Through its Rhodes Interform business, it has also developed a stamping process that enables large monocoque components, particularly those produced by super plastic forming (SPF) from very thin material, to accurately retain their shape on cooling. The company designs, manufactures and installs titanium and aluminium forming cells for aerospace and automotive manufacturers.
Dualform is a patented process incorporating a special Double Acting Hydraulic Press. This process enables the simultaneous manufacture of matched top and bottom dies within the press, which in turn are used for the manufacture of finished pressed panels. Group Rhodes, based in West Yorkshire (UK), has won Queen’s Awards for both Innovation and International Trade in recent years, particularly for its work in the aerospace sector.
To read the rest of this article in the February 2025 issue of ISMR, see https://joom.ag/AbMd/p48