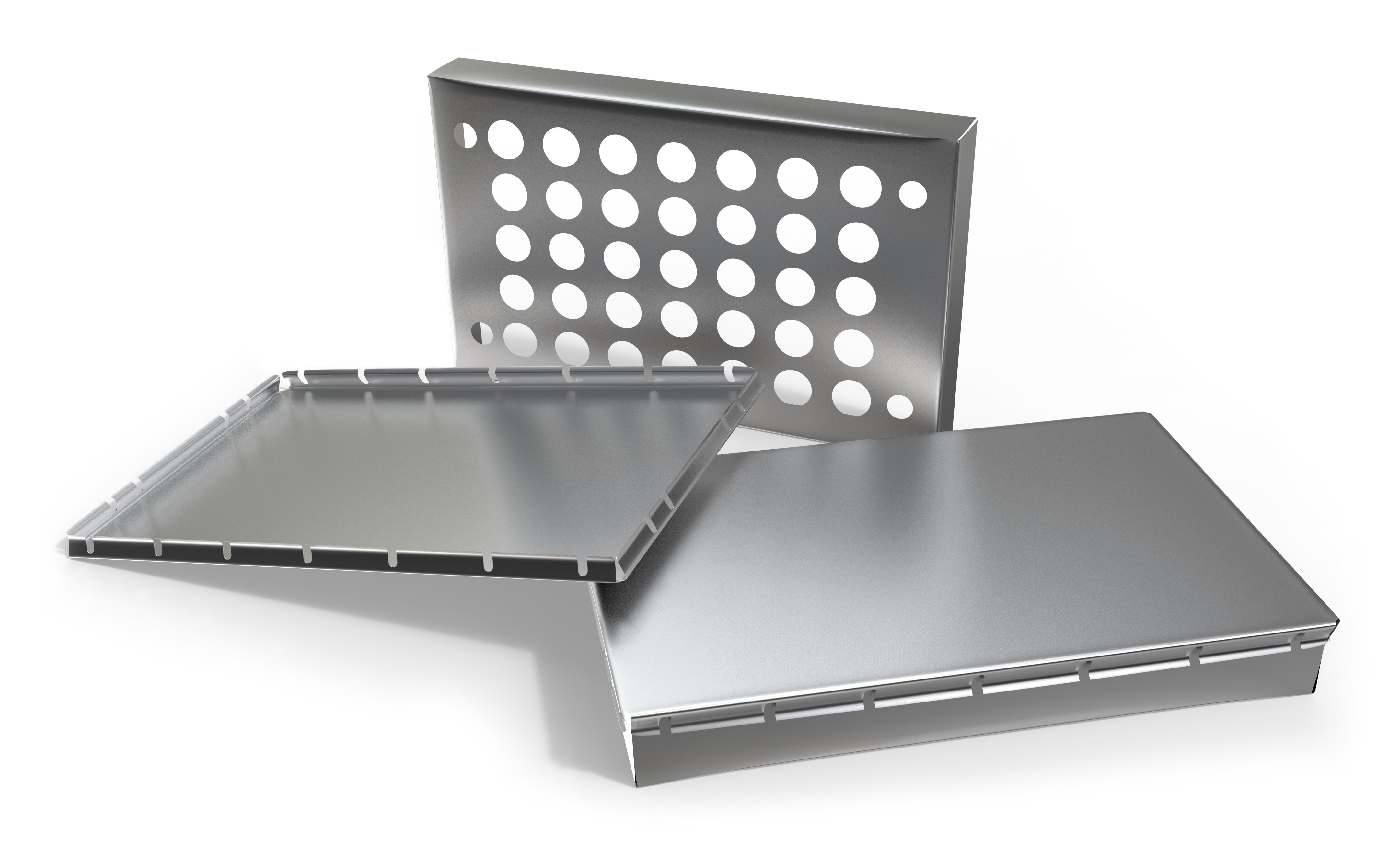
Sourcing large enclosures
Submitted by:
Sara Waddington
What should you look for when sourcing large sheet metal enclosures? Tenere Inc. outlines some pointers to keep in mind for your next project, in the June 2022 issue of International Sheet Metal Review magazine.
++++++++++++++
Sheet metal enclosures come in all shapes and sizes. It’s the larger ones, however, that can sometimes cause designers and manufacturers the most grief.
Many challenges come with designing and manufacturing large structures. Without reinforcement, the walls and ceiling tend to bow. Moving them around when complete is next to impossible, so building large structures near their final home is a good idea. Duct tape and glue only go so far at holding it all together, so sound joining techniques are essential. It’s arduous work, even for the craftiest kids on the block.
Similar statements can be made about super-sized custom metal fabrications. These include data centre solutions such as server racks and cabinets. There are steel enclosures for fibre optics, battery storage and edge computing hardware. Retail kiosks and ATMs are common in this sector, as are OCP (open compute project) solutions. These, and other custom sheet metal enclosures, serve many critical industrial applications.
It is essential to recognize that, no matter how good your design is, not all manufacturers are up to the task.
High-tech manufacturing and automated processes
The fabrication of large sheet metal enclosures comes with unique challenges as opposed to smaller part production. For example, the panels on the sides and backs of fabricated enclosures are often too large to bend on a press brake or require multiple operators (more labour costs). An alternative would be to use a panel bender, which allows the metal sheet to lie flat during processing for a high-quality bend.
Integrated sheet metal automation is another essential capability to keep in mind. Robotic welding helps to reduce fabricating costs, as do automated material handling systems such as conveyors and sheet loaders. These also improve working conditions, eliminating the risk of injury when handling large steel, aluminium and stainless-steel sheets.
Capabilities such as in-floor lifting systems or cranes, bring the work to those performing operations in the factory like spot welding; riveting; buffing and polishing; and final assembly. These automated systems help to make the manufacturing process more efficient, giving customers high-quality products.
To read the rest of this article, see https://joom.ag/zRad/p38